New technique for manufacturing high alloy steel seamless pipe with heavy calibre by adopting pilger mill
A high-alloy steel, seamless tube technology, applied in the direction of manufacturing tools, metal rolling, metal processing equipment, etc., can solve the problems of dimensional accuracy, surface quality, high cost, long process, etc. Equipment investment and operating costs, as well as the effect of floor space, reduced workload, and short process flow
- Summary
- Abstract
- Description
- Claims
- Application Information
AI Technical Summary
Benefits of technology
Problems solved by technology
Method used
Image
Examples
Embodiment Construction
[0042] Such as image 3 Shown is a process flow diagram of an embodiment of the present invention, which specifically includes the following process steps:
[0043] In the first step, the high-pressure boiler tube refined outside the furnace is centrifugally cast with P22 molten steel into a hollow tube blank of Φ871x128mm through a centrifugal casting machine. In this step, the molten steel refined outside the furnace is the same as the prior art, and will not be repeated here; the centrifugal casting is carried out on a horizontal centrifugal casting machine with an angle of 0 degrees between the rotation axis of the mold and the horizontal. The cast hollow tube blank is a hollow tube blank with equal wall thickness and transparent ends. Using the centrifugal casting machine can conveniently and high-quality process the hollow tube billet used in the next step, without the need for heating, piercing and reaming of the continuous casting steel ingot in the prior art, which n...
PUM
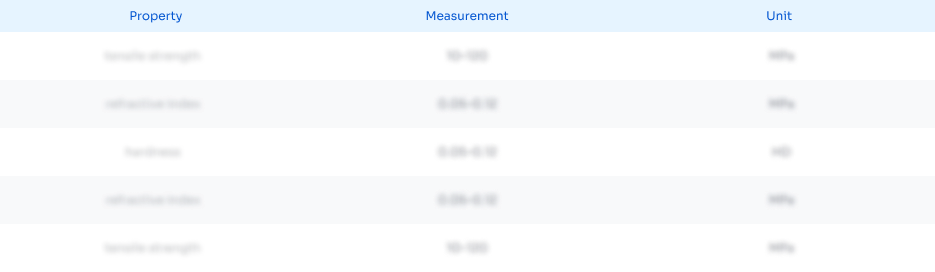
Abstract
Description
Claims
Application Information

- Generate Ideas
- Intellectual Property
- Life Sciences
- Materials
- Tech Scout
- Unparalleled Data Quality
- Higher Quality Content
- 60% Fewer Hallucinations
Browse by: Latest US Patents, China's latest patents, Technical Efficacy Thesaurus, Application Domain, Technology Topic, Popular Technical Reports.
© 2025 PatSnap. All rights reserved.Legal|Privacy policy|Modern Slavery Act Transparency Statement|Sitemap|About US| Contact US: help@patsnap.com