Bionic leg with three-dimensional force perception and spatial surface self-adaptive ability
A three-dimensional force and self-adaptive technology, applied in the field of robotics, can solve the problems of complex structure design, calculation principle and manufacturing, complex design principle and processing technology, and difficulty in three-dimensional force detection of robots. handy effect
Inactive Publication Date: 2010-12-01
NANJING UNIV OF AERONAUTICS & ASTRONAUTICS
View PDF9 Cites 0 Cited by
- Summary
- Abstract
- Description
- Claims
- Application Information
AI Technical Summary
Problems solved by technology
At present, the research on three-dimensional force sensors at home and abroad is mainly used in robot technology. According to the principle of force measurement, it can be divided into resistance strain type, capacitive type, piezoelectric type and photoelectric type. According to the elastic body structure, it can be divided into direct output type and indirect output type. , but the design principle and processing technology are more complicated
In the design of elastomer structures, beam structures (patent 200810025591.2, Han Yulin, etc.), barrel structures (patent 200610016178.0, Liu Bo, etc.), frame structures (patent 03112680.4, Song Aiguo, etc.) are mainly used. Although all of them can realize three-dimensional force detection, However, the structural design, calculation principle and manufacturing are relatively complicated, mainly due to the fact that the structure is not compact enough, and it is difficult to be used in the three-dimensional force detection of micro-miniature robots and the integrated small design of the leg structure.
Method used
the structure of the environmentally friendly knitted fabric provided by the present invention; figure 2 Flow chart of the yarn wrapping machine for environmentally friendly knitted fabrics and storage devices; image 3 Is the parameter map of the yarn covering machine
View moreImage
Smart Image Click on the blue labels to locate them in the text.
Smart ImageViewing Examples
Examples
Experimental program
Comparison scheme
Effect test
Embodiment Construction
the structure of the environmentally friendly knitted fabric provided by the present invention; figure 2 Flow chart of the yarn wrapping machine for environmentally friendly knitted fabrics and storage devices; image 3 Is the parameter map of the yarn covering machine
Login to View More PUM
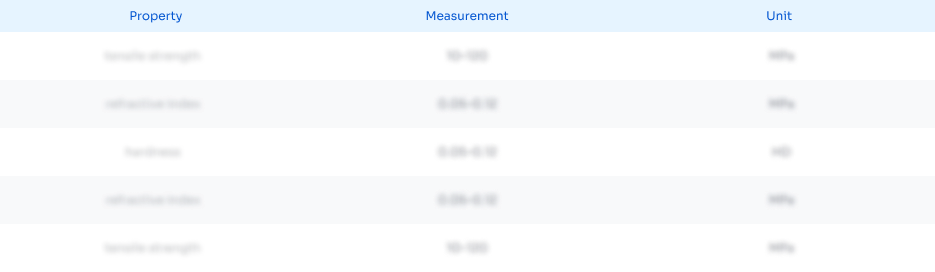
Abstract
The invention relates to a bionic leg with three-dimensional force perception and spatial surface self-adaptive ability, which belongs to the field of application of robot technology. The bionic leg comprises a robot base (1), a hip joint, a thigh (3), a knee joint, a crus and a foot, wherein the hip joint comprises a No.I hip joint control actuator (2), a hip joint control actuator bracket (4) and a No.II hip joint control actuator (5); the knee joint comprises a knee joint control actuator (7) and a knee joint control actuator bracket (6); the crus comprises a connecting plate (8) and a three-dimensional force sensor (9); and the foot comprises a return spring (10), a globe joint and a sole (14). The bionic leg can be applied to the integrated design of a human leg part of multiple degrees of freedom microminiature leg-type robot which has three-dimensional contact force detection and the ability of a self-adaptive spatial surface adhesion sole.
Description
Bionic leg with three-dimensional force perception and spatial surface adaptation technical field The invention belongs to the application field of robot technology, in particular to a bionic leg with three-dimensional force perception and space surface self-adaptive ability, which is mainly used in the realization of legged robot motion. Background technique Legged robots at home and abroad can include bipeds, quadrupeds, hexapods, eight-legged robots, etc. In the structural design, a single leg of a biped robot has 6 actively driven degrees of freedom, while in quadruped, hexapod, and octaped robots, due to the large number of legs, the degree of freedom of a single leg is generally 3 actively driven. Degree of freedom, the foot end of the leg adopts point contact or ball contact mode (patent 200710098710.2 Luo Qingsheng etc.). For a multi-legged robot that climbs walls or adheres to walking, the robot's legs need to have more degrees of freedom to adapt to different su...
Claims
the structure of the environmentally friendly knitted fabric provided by the present invention; figure 2 Flow chart of the yarn wrapping machine for environmentally friendly knitted fabrics and storage devices; image 3 Is the parameter map of the yarn covering machine
Login to View More Application Information
Patent Timeline

Patent Type & Authority Patents(China)
IPC IPC(8): B62D57/032
Inventor 俞志伟戴振东李宏凯张昊阮鹏张晓峰
Owner NANJING UNIV OF AERONAUTICS & ASTRONAUTICS
Features
- R&D
- Intellectual Property
- Life Sciences
- Materials
- Tech Scout
Why Patsnap Eureka
- Unparalleled Data Quality
- Higher Quality Content
- 60% Fewer Hallucinations
Social media
Patsnap Eureka Blog
Learn More Browse by: Latest US Patents, China's latest patents, Technical Efficacy Thesaurus, Application Domain, Technology Topic, Popular Technical Reports.
© 2025 PatSnap. All rights reserved.Legal|Privacy policy|Modern Slavery Act Transparency Statement|Sitemap|About US| Contact US: help@patsnap.com