Finite element modeling method used for damage process of thermal barrier coating of turbine blade
A technology for turbine blades and thermal barrier coatings, applied in the field of high-performance aero-engine thermal insulation and protective coating systems, can solve problems such as limited modeling capabilities, difficulty in building object models, and cumbersome operations, and achieve clear thinking, easy to master and Use, overcome the effects of incompatibility
Active Publication Date: 2011-01-05
XIANGTAN UNIV
View PDF0 Cites 0 Cited by
- Summary
- Abstract
- Description
- Claims
- Application Information
AI Technical Summary
Problems solved by technology
However, the general-purpose finite element software program has very limited geometric modeling capabilities, and it is difficult to establish object models with complex geometric structures, and its workload is very large, and the operation is cumbersome. Therefore, it is urgent to develop related finite element special pre-processing methods and skills to accomplish
After checking the existing technology, there is no report on the finite element simulation research on the damage process of the turbine blade thermal barrier coating system with the actual shape of the complex curved surface
Method used
the structure of the environmentally friendly knitted fabric provided by the present invention; figure 2 Flow chart of the yarn wrapping machine for environmentally friendly knitted fabrics and storage devices; image 3 Is the parameter map of the yarn covering machine
View moreImage
Smart Image Click on the blue labels to locate them in the text.
Smart ImageViewing Examples
Examples
Experimental program
Comparison scheme
Effect test
Embodiment 1
Embodiment 2
the structure of the environmentally friendly knitted fabric provided by the present invention; figure 2 Flow chart of the yarn wrapping machine for environmentally friendly knitted fabrics and storage devices; image 3 Is the parameter map of the yarn covering machine
Login to View More PUM
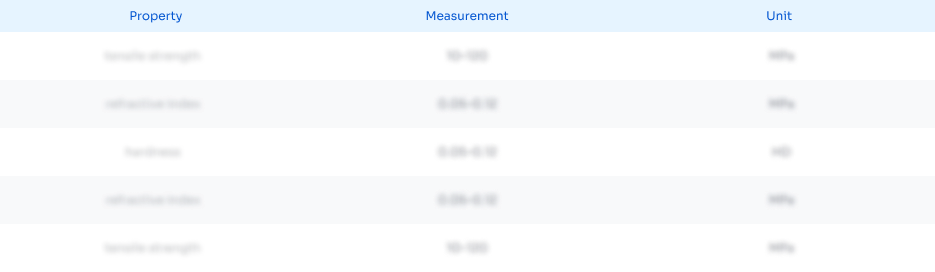
Abstract
The invention discloses a finite element modeling method used for damage processes of the thermal barrier coating of a turbine blade, belonging to the field of heat-insulation protection coating system technology of high-performance aero-engine. The method adopts a CATIA software and a finite element ABAQUS software. The method wholly models all coatings and the substrate in the CATIA software, carries out a secondary processing to geometrical models in the ABAQUS software, carries out geometrical cleaning to the model in the CATIA software, and carries out simulation, calculation and result analysis in the ABAQUS software. The method can effectively overcome the incompatibility of the CAD software such as CATIA and the like and the finite element software, considers both various properties of the heat barrier coating material and the geometrical shape of the substrate, can exactly simulate the relevant key physical quantity of the turbine blade heat barrier coating system in practicalworking environment, has clear concept and is convenient to be mastered and used by the technicians.
Description
Finite Element Modeling Method for Failure Process of Turbine Blade Thermal Barrier Coating System technical field The invention belongs to the technical field of high-performance aero-engine thermal barrier coating systems, and in particular relates to a finite element modeling method for the destruction process of a turbine blade thermal barrier coating system. Background technique Thermal barrier coatings (TBCs for short) are based on the characteristics of high melting point, low thermal conductivity, low vapor pressure, low emissivity and high reflectivity of ceramic materials. Ceramic powder is sprayed or deposited on superalloy hot end parts (especially turbines Blade) surface to reduce the working temperature of high-temperature components, so as to protect them from high-temperature corrosion and high-temperature oxidation, greatly prolonging the service life of high-temperature components, so that the high-temperature alloy components in modern aviation gas turbin...
Claims
the structure of the environmentally friendly knitted fabric provided by the present invention; figure 2 Flow chart of the yarn wrapping machine for environmentally friendly knitted fabrics and storage devices; image 3 Is the parameter map of the yarn covering machine
Login to View More Application Information
Patent Timeline

Patent Type & Authority Patents(China)
IPC IPC(8): G06F17/50G06T19/00
Inventor 周益春刘奇星毛卫国蒋俊平
Owner XIANGTAN UNIV
Features
- R&D
- Intellectual Property
- Life Sciences
- Materials
- Tech Scout
Why Patsnap Eureka
- Unparalleled Data Quality
- Higher Quality Content
- 60% Fewer Hallucinations
Social media
Patsnap Eureka Blog
Learn More Browse by: Latest US Patents, China's latest patents, Technical Efficacy Thesaurus, Application Domain, Technology Topic, Popular Technical Reports.
© 2025 PatSnap. All rights reserved.Legal|Privacy policy|Modern Slavery Act Transparency Statement|Sitemap|About US| Contact US: help@patsnap.com