Luminaire control system and method
A controller, coordinate system technology, applied in the field of lighting
- Summary
- Abstract
- Description
- Claims
- Application Information
AI Technical Summary
Problems solved by technology
Method used
Image
Examples
example 1
[0053] In a first instance, the control system can be configured to read RGB sensor data [RGB] and apply a predetermined transformation to derive approximations of the CIE tristimulus values X, Y and Z of the light emitted by the LEE. This can be performed, for example, by programming the control system using the linear algebraic relationship
[X Y Z]=[R G B]T (3)
Use a 3×3 transformation matrix
T=(N T N) -1 N T M=N + M (4)
N T is the transpose and N + is the pseudo-inverse of N. M is the ideal three-color excitation value M ij The n×3 matrix of and N is the corresponding n×3 matrix of RGB color sensor data for the same set of n SPDs. M and N can be determined during a calibration step using n SPDs and characterizing them with RGB color sensors to determine N and, for example, M with a precisely calibrated spectrometer. Next determine T by the minimum error function e.g. by the least squares solution
This approach can provide a way to mitigate the average...
example 2
[0060] In another embodiment, it may be advantageous in terms of computational efficiency to operate the control system directly using the feedback raw RGB sensor data. In such an embodiment, the control system no longer has to transform RGB sensor data every time that data is fed back. Instead, user-specified input data is transformed from coordinates such as, for example, XYZ tristimulus or xyY chromaticity and intensity to RGB sensor coordinates so that the control system compares the adjustment points with the RGB color feedback data. In such an embodiment, the transformation needs to occur only when the user specifies that the input data changes. In this embodiment the control system operates in RGB sensor coordinates to set and maintain desired chromaticity and intensity.
[0061] For a predetermined transformation T, the target RGB values can be determined from the following equation:
[R T G T B T ]=[X Y Z]T -1 (11)
It should be noted that t...
example 3
[0063]In this embodiment the controller is configured to transform each of the one or more predetermined RGB sensor data into a respective predetermined desired color space, e.g. XYZ data while transforming the remaining RGB sensor data as described above The training set, even though the mean least squared error of the remaining data is increased. This embodiment can be used to ensure that the control system is able to perform a calibration process that maintains white light RGB sensor data.
[0064] Additional constraints on the calibration method can be expressed as M w =N w T, where N w is the RGB sensor data for the intended "white" SPD, and M w is the corresponding XYZ tristimulus value. The transformation matrix can be determined by the following equation:
T j = ( N T N ) - ...
PUM
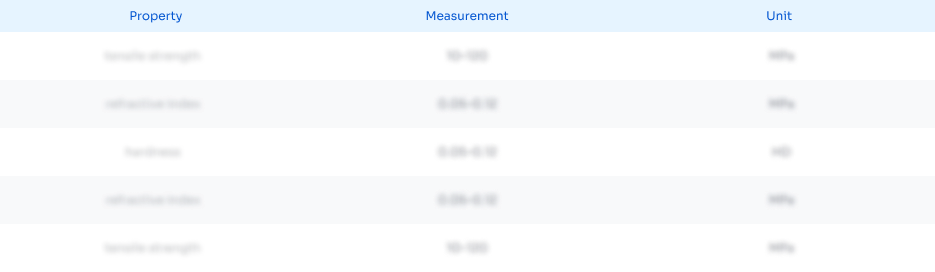
Abstract
Description
Claims
Application Information

- Generate Ideas
- Intellectual Property
- Life Sciences
- Materials
- Tech Scout
- Unparalleled Data Quality
- Higher Quality Content
- 60% Fewer Hallucinations
Browse by: Latest US Patents, China's latest patents, Technical Efficacy Thesaurus, Application Domain, Technology Topic, Popular Technical Reports.
© 2025 PatSnap. All rights reserved.Legal|Privacy policy|Modern Slavery Act Transparency Statement|Sitemap|About US| Contact US: help@patsnap.com