Method for separating cellulose from straws and getting cellulose solution
A cellulose and aqueous solution technology, which is applied in fiber raw material processing, textile and papermaking, etc., can solve the problems of lack of research on straw cellulose, and achieve the effects of saving dosage, reducing pollution and reducing costs.
- Summary
- Abstract
- Description
- Claims
- Application Information
AI Technical Summary
Problems solved by technology
Method used
Image
Examples
Embodiment 1
[0021] figure 1 A schematic flow chart of the present invention for separating cellulose from straw and preparing cellulose aqueous solution is given: the whole process is divided into three steps: firstly, the raw material straw biomass A is subjected to acid pretreatment to remove hemicellulose, and after filtration and separation, Obtain hemicellulose-degraded sugar solution C and residue B; then carry out delignification treatment on residue B to obtain pure cellulose D; finally dissolve the obtained cellulose with alkaline water solvent to obtain cellulose aqueous solution E. These three steps are interrelated, that is: the removal rate of hemicellulose in the first step should be greater than 85%, so as to ensure the smooth progress of the second step delignification step; similarly, the removal of lignin in the second step The ratio should be greater than 80% of its original content to ensure that the obtained cellulose has sufficient purity, and at the same time to ens...
Embodiment 2
[0041] In this example, 10 grams of dewaxed bagasse powder was first added to the reactor, and 150 ml of phosphoric acid aqueous solution with a concentration of 8 mol / L was added, followed by reaction at 80° C. for 3 hours. After cooling, it was filtered, and the filter cake was washed with deionized water and ethanol, and dried at 55°C. Add subsequently in the aqueous solution of 25% PEG-4000 in 100 milliliters, also contain 7.0wt% NaOH, 3.9wt% NaOH simultaneously in this aqueous solution 2 S and 2.1 wt% Na 2 CO 3 . Heat the reaction at 180° C. for 1.5 hours, then cool, filter, wash, and dry to obtain cellulose powder.
[0042] Add 3 grams of the resulting cellulose powder into 50 milliliters of a mixture aqueous solution of 4-10wt% lithium hydroxide / 4-15wt% urea (or 4-15wt% thiourea) as a solvent, stir for 30 minutes, and put Pre-cool in a refrigerator at -20°C for 12 hours, take out and melt, and stir until a uniform cellulose solution is obtained.
Embodiment 3
[0044] In this example, 12 grams of dewaxed rice straw powder was first added to the reactor, and 200 ml of sulfuric acid aqueous solution with a concentration of 2 mol / L was added, and then reacted at 100° C. for 5 hours. After cooling, it was filtered, and the filter cake was washed with deionized water and ethanol, and dried at 55°C. Add subsequently in the aqueous solution of 30% PEG-500 in 150 milliliters, also contain 7.0wt% NaOH, 3.1wt%wt%Na in this aqueous solution simultaneously 2 S and 2.1 wt% Na 2 CO 3 . Heat the reaction at 100°C for 6 hours, then cool, filter, wash, and dry to obtain cellulose powder.
[0045] Add 3 grams of the cellulose powder obtained above to 80 milliliters of a mixture aqueous solution of 4-10wt% lithium hydroxide / 4-15wt% urea (or 4-15wt% thiourea) as a solvent, stir for 30 minutes, and put Pre-cool in a refrigerator at -20°C for 12 hours, then remove and melt, and combine with vigorous stirring to obtain a uniform cellulose solution.
PUM
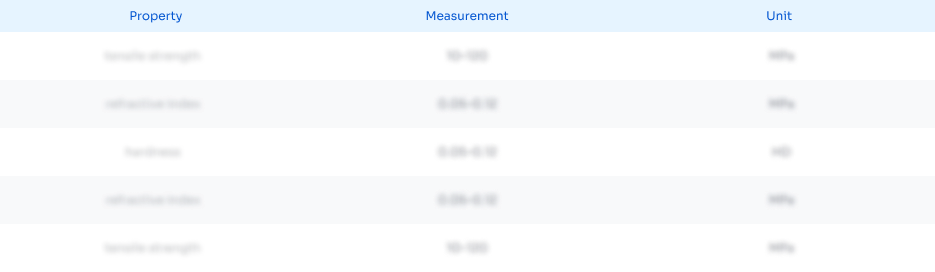
Abstract
Description
Claims
Application Information

- Generate Ideas
- Intellectual Property
- Life Sciences
- Materials
- Tech Scout
- Unparalleled Data Quality
- Higher Quality Content
- 60% Fewer Hallucinations
Browse by: Latest US Patents, China's latest patents, Technical Efficacy Thesaurus, Application Domain, Technology Topic, Popular Technical Reports.
© 2025 PatSnap. All rights reserved.Legal|Privacy policy|Modern Slavery Act Transparency Statement|Sitemap|About US| Contact US: help@patsnap.com