Method for producing anticorrosive oil composition
A production method and composition technology, applied in lubricating compositions, petroleum industry, base materials, etc., can solve the problems of long production time of anti-rust oil composition, easy excessive oxidation of oil products, affecting anti-rust effect, etc., and achieve shortening Production time, shortened production time, and the effect of preventing excessive oxidation
- Summary
- Abstract
- Description
- Claims
- Application Information
AI Technical Summary
Problems solved by technology
Method used
Image
Examples
Embodiment 1
[0022] Add 500 kg of twice-hydrogenated mineral oil HV II2 (produced by Sinopec Shanghai Gaoqiao Branch) into the blending kettle and heat to 60°C; add magnesium petroleum sulfonate, sodium petroleum sulfonate, and calcium petroleum sulfonate with medium alkalinity , dodecenyl succinate monoester, heptadecenyl imidazolidinyl succinate, 2,6-di-tert-butyl p-cresol, continue heating to 110°C, and stir at constant temperature for 4 hours. Then add 350 kg of twice hydrogenated mineral oil HV II2, stir evenly, and circulate and filter with a suction filter until the oil temperature drops to 75°C for canning. Each component and its weight percentage are shown in Table 1, and the product properties are shown in Table 2.
Embodiment 2
[0024] Add 550 kg of No. 10 transformer oil into the blending kettle and heat it to 65°C; add magnesium petroleum sulfonate, sodium petroleum sulfonate, calcium petroleum sulfonate with high alkali value, zinc naphthenate, dodecenylsuccinic acid mono Esters, 2,6-di-tert-butyl-a-dimethylamino-p-cresol, and nonylphenol polyoxyethylene (4) ether were heated to 115°C and stirred at constant temperature for 2.5 hours. Then add 300 kg of No. 10 transformer oil, stir evenly, and circulate and filter with a suction filter until the oil temperature drops to 75°C for canning. Each component and its weight percentage are shown in Table 1, and the product properties are shown in Table 2.
Embodiment 3
[0026]Add 600kg of HVI75SN into the blending kettle and heat to 80°C; add petroleum magnesium sulfonate, nonylphenol ether phosphate, high alkali value calcium petroleum sulfonate, zinc naphthenate, dodecenyl succinate monoester , N-amino-a-naphthylamine, pentaerythritol oleate, continue heating to 120°C, and stir at constant temperature for 2 hours. Then add 240 kg of base oil, stir evenly, and circulate and filter with a suction filter until the oil temperature drops to 75°C for canning. Each component and its weight percentage are shown in Table 1, and the product properties are shown in Table 2.
PUM
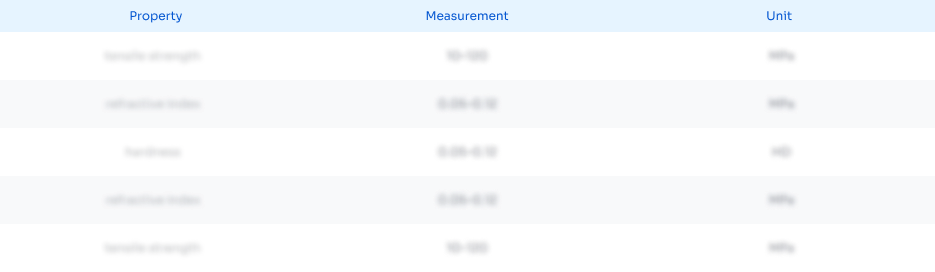
Abstract
Description
Claims
Application Information

- R&D
- Intellectual Property
- Life Sciences
- Materials
- Tech Scout
- Unparalleled Data Quality
- Higher Quality Content
- 60% Fewer Hallucinations
Browse by: Latest US Patents, China's latest patents, Technical Efficacy Thesaurus, Application Domain, Technology Topic, Popular Technical Reports.
© 2025 PatSnap. All rights reserved.Legal|Privacy policy|Modern Slavery Act Transparency Statement|Sitemap|About US| Contact US: help@patsnap.com