External cowling of scramjet engine and design method thereof
A scramjet and external rectification technology, applied in aircraft parts, aircraft power units, aircraft power unit components, etc., can solve the problems of improving and affecting the lift-to-drag ratio of the aircraft, unfavorable to the lift-drag ratio of the aircraft, and reduce the headwind. Area, good aerodynamic performance, the effect of reducing drag
- Summary
- Abstract
- Description
- Claims
- Application Information
AI Technical Summary
Problems solved by technology
Method used
Image
Examples
Embodiment 1
[0025] Such as Figure 1a with 1b The two-dimensional schematic diagram of the hypersonic vehicle shown. The entire aircraft can be divided into three main parts: the front body, the engine and the rear body. In the existing design, the outer fairing part of the engine adopts Figure 1a In the common fairing design scheme, the outer fairing of the present invention is as Figure 1b with figure 2 As shown, it includes a side plate 2 and a bottom plate 1, the bottom plate 1 is a rectangular plate, and protrudes upwards to form an arc-shaped cover, which is formed by protruding along the direction of the lip 11 of the bottom plate to the opposite side of the lip 11, and the front of the aircraft The high-pressure area generated by the body-induced shock wave is basically wrapped under the lower wall of the arc-shaped cover formed by the bottom plate 1, so the high-pressure area behind the shock wave can generate additional lift for the aircraft, and the two side plates 2 are a...
Embodiment 2
[0027] The design method of scramjet outer fairing of the present invention, concrete steps are:
[0028] 1) Under the condition of hypersonic flight, first conduct an inviscid analysis on the flow field of the aircraft to obtain detailed data of the flow field and the exact position of the shock wave;
[0029] 2) Starting from the lip of the engine inlet, follow the streamline equation along the incoming flow direction, and the curved surface formed by all the streamlines constitutes the lower wall of the engine outer fairing bottom plate;
[0030] 3) The two side plates of the outer fairing are relatively arranged on the bottom plate, and the side wall surface of the side plate can be a plane perpendicular to the lower wall surface of the bottom plate;
[0031] 4) According to the incoming flow conditions, deflect the outer fairing counterclockwise along point A of the lip (see Figure 1b ), the specific deflection angle can be obtained by calculation or experiment accordin...
PUM
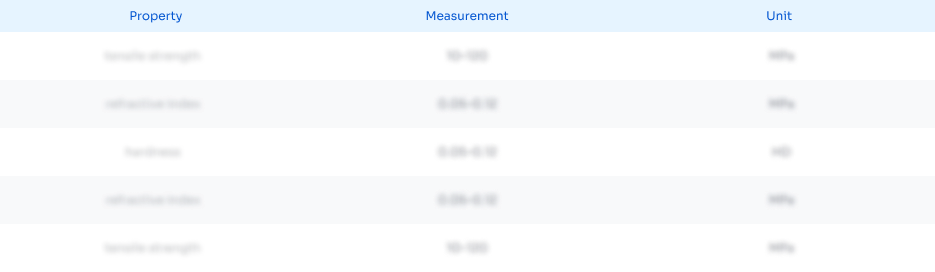
Abstract
Description
Claims
Application Information

- Generate Ideas
- Intellectual Property
- Life Sciences
- Materials
- Tech Scout
- Unparalleled Data Quality
- Higher Quality Content
- 60% Fewer Hallucinations
Browse by: Latest US Patents, China's latest patents, Technical Efficacy Thesaurus, Application Domain, Technology Topic, Popular Technical Reports.
© 2025 PatSnap. All rights reserved.Legal|Privacy policy|Modern Slavery Act Transparency Statement|Sitemap|About US| Contact US: help@patsnap.com