Bamboo fiber grinding device
A technology of roller compactor and bamboo fiber, applied in the direction of wood processing utensils, manufacturing tools, etc., can solve the problems of undisclosed compaction, large gap during stacking, low added value of products, etc., and achieves good impregnation permeability, manufacturing The effect of cost reduction and production process simplification
- Summary
- Abstract
- Description
- Claims
- Application Information
AI Technical Summary
Problems solved by technology
Method used
Image
Examples
Embodiment Construction
[0012] The structure of the present invention is made up of frame (1), electric motor, speed reducer, transmission mechanism, bearing seat, the upper and lower wheel roller (10) that is installed on the bearing seat.
[0013] The outer profile of the wheel roller is not tooth-shaped but cylindrical, the bearing seat (5) of the lower wheel roller (10) is fixed on the frame (1), and the bearing seat (4) of the upper wheel roller (6) is installed on the On the sliding track (3) of the frame (1), a compression spring (2) is fixed on the bearing seat, and the other end of the compression spring (2) is fixed on the frame (1), and the transmission mechanism is the output wheel on the output shaft of the reducer (11) and the lower wheel roller (10) center distance sprocket or pulley transmission, the output wheel (11) on the output shaft of the reducer and the upper wheel roller (6) can adjust the sprocket or pulley transmission, and the adjustable transmission is two A tension pulley...
PUM
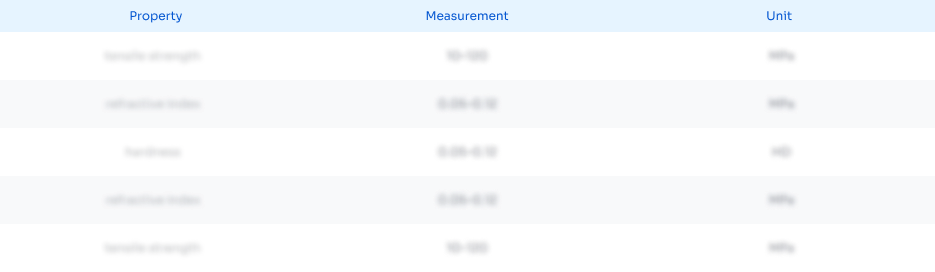
Abstract
Description
Claims
Application Information

- R&D Engineer
- R&D Manager
- IP Professional
- Industry Leading Data Capabilities
- Powerful AI technology
- Patent DNA Extraction
Browse by: Latest US Patents, China's latest patents, Technical Efficacy Thesaurus, Application Domain, Technology Topic, Popular Technical Reports.
© 2024 PatSnap. All rights reserved.Legal|Privacy policy|Modern Slavery Act Transparency Statement|Sitemap|About US| Contact US: help@patsnap.com