Full automatic coiled sheet material energy-saving blanking machine
A fully automatic, unloading machine technology, applied in the cutting of textile materials, shoemaking machinery, clothing, etc., can solve problems such as low work efficiency, operator hand damage, waste of raw materials, etc., to improve production efficiency and ensure Product quality, the effect of saving raw materials
- Summary
- Abstract
- Description
- Claims
- Application Information
AI Technical Summary
Problems solved by technology
Method used
Image
Examples
Embodiment Construction
[0018] Below in conjunction with accompanying drawing and embodiment the technical scheme of the present invention is further described
[0019] exist figure 1 Middle: The conveyor belt chain (4) on the discharge table (1) is connected with the conveying roller sprocket (24) on the host machine (2), and the host machine (2) is linked with the feed table frame (10). The workbench frame (10) is connected with the coil feeder (11), the cylinder (3) is connected with the pressure roller (5), and the main shaft of the stepping motor (9) is provided with a sprocket (21) and an overrunning clutch. Close to the outside of the sprocket (21) is an overrunning clutch, one end of the frame chain (8) is connected with the overrunning clutch, and the other end is connected with the sprocket of the conveyor belt (23) on the feeding table frame (10) , conveyor belt (23) if retrogression occurs, the overrunning clutch is just very slippery, and the limit goes backwards, guarantees the normal ...
PUM
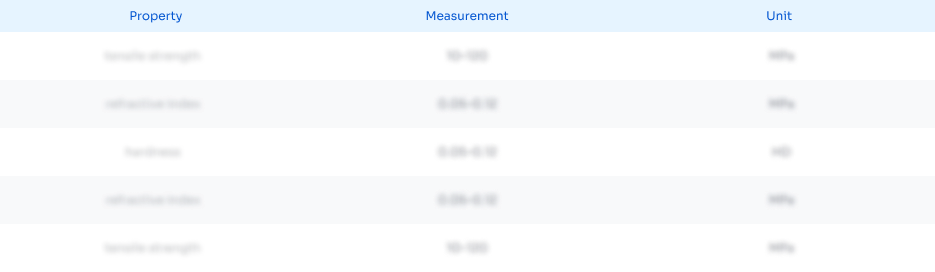
Abstract
Description
Claims
Application Information

- R&D
- Intellectual Property
- Life Sciences
- Materials
- Tech Scout
- Unparalleled Data Quality
- Higher Quality Content
- 60% Fewer Hallucinations
Browse by: Latest US Patents, China's latest patents, Technical Efficacy Thesaurus, Application Domain, Technology Topic, Popular Technical Reports.
© 2025 PatSnap. All rights reserved.Legal|Privacy policy|Modern Slavery Act Transparency Statement|Sitemap|About US| Contact US: help@patsnap.com