Core assembly and core assembling technique thereof
A technology of core group and core assembly, which is applied in the direction of cores, manufacturing tools, metal processing equipment, etc., can solve problems such as easy generation of air holes, large operation difficulty, difficulty in ensuring casting size, etc., to reduce casting defects and increase operability , the effect of high dimensional accuracy
- Summary
- Abstract
- Description
- Claims
- Application Information
AI Technical Summary
Problems solved by technology
Method used
Image
Examples
Embodiment Construction
[0013] like figure 1 The shown core group includes a plurality of cavity cores 21 which are provided with series connection holes and connected in series through the series connection holes, upper shape cores 22 and lower shape cores 22 respectively arranged at both ends of the plurality of cavity cores 21 connected in series. Outline core 23, successively pass through upper shape core 22, multiple cavity cores 21, serial connector 28 of lower shape core 23, be arranged on the two ends of serial connector 28 and be used for fastening serial connection in serial connector 28 on the upper profile core 22, multiple cavity cores 21, fasteners 24 of the lower profile core 23, respectively arranged on the upper profile core 22, multiple cavity cores 21, left side edge cores 25 on both sides of the lower profile core 23 And right side side core 26. like image 3 As shown, the connecting parts between the upper profile core 22, the right side core 26, the lower profile core 23, and ...
PUM
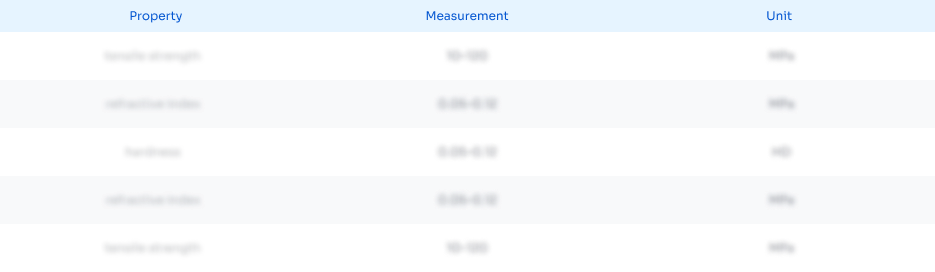
Abstract
Description
Claims
Application Information

- R&D
- Intellectual Property
- Life Sciences
- Materials
- Tech Scout
- Unparalleled Data Quality
- Higher Quality Content
- 60% Fewer Hallucinations
Browse by: Latest US Patents, China's latest patents, Technical Efficacy Thesaurus, Application Domain, Technology Topic, Popular Technical Reports.
© 2025 PatSnap. All rights reserved.Legal|Privacy policy|Modern Slavery Act Transparency Statement|Sitemap|About US| Contact US: help@patsnap.com