Method for producing high-solid content low-viscosity polymer polylol
A technology with high solid content and polyols, which is applied in the field of low viscosity polymer polyols, batch and continuous methods to prepare high solid content, and can solve problems such as high product viscosity, blocked pipes, and high toxicity of tetramethylsuccinonitrile
- Summary
- Abstract
- Description
- Claims
- Application Information
AI Technical Summary
Problems solved by technology
Method used
Image
Examples
preparation example Construction
[0027] The preparation method of polymer polyol:
[0028] Method 1: Add most of the basic polyether polyol A into a reaction kettle equipped with a stirring device, a feeder, and a thermometer, and replace with nitrogen three times to make the oxygen content in the system meet the experimental requirements. Under the protection of nitrogen, the temperature of the materials in the reactor was raised, and when the temperature was stabilized at 115° C., the materials were fed at a certain feeding speed. The feed was formulated from the remaining base polyether A, styrene, acrylonitrile, free radical initiator, dispersant and chain transfer agent. After the feeding is completed, ripen for 2 hours and degas under reduced pressure for 2 hours. During the whole reaction process, the temperature is preferably controlled at 115±5°C. Cool down and discharge.
[0029] Method 2: Add a certain amount of polymer polyol with target solid content into a reaction kettle equipped with a stirr...
specific example 1
[0030] Concrete example 1: adopt method 1, add basic polyether polyol A 240g in the reactor, nitrogen replacement three times, and make the material in the reactor warm up under the protection of nitrogen, when the temperature reaches 115 ℃, according to a certain feeding speed, enter material. Feed composition: 100g of acrylonitrile, 229g of styrene, 2.2g of initiator, 2.8g of chain transfer agent, 21g of dispersant SA-01, and 105g of basic polyether polyol A. The residence time was controlled at 60 minutes, and after the feeding was completed, it was matured for 2 hours, degassed under reduced pressure, cooled and discharged to obtain polymer polyol A.
specific example 2
[0031] Concrete example 2: adopt method 1, add basic polyether polyol A 240g in the reaction kettle, nitrogen replacement three times, and make the material in the reaction kettle warm up under the protection of nitrogen, when the temperature reaches 115 ℃, feed in at a certain feeding speed material. Feed composition: 100g of acrylonitrile, 229g of styrene, 2.2g of initiator, 2.8g of chain transfer agent, 21g of dispersant SA-02, and 105g of basic polyether polyol A. The residence time was controlled at 60 minutes, and after the feeding was completed, it was matured for 2 hours, degassed under reduced pressure, cooled and discharged to obtain the polymer polyol B.
PUM
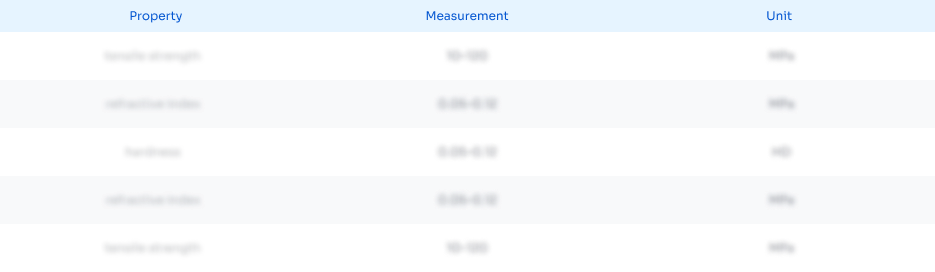
Abstract
Description
Claims
Application Information

- R&D Engineer
- R&D Manager
- IP Professional
- Industry Leading Data Capabilities
- Powerful AI technology
- Patent DNA Extraction
Browse by: Latest US Patents, China's latest patents, Technical Efficacy Thesaurus, Application Domain, Technology Topic, Popular Technical Reports.
© 2024 PatSnap. All rights reserved.Legal|Privacy policy|Modern Slavery Act Transparency Statement|Sitemap|About US| Contact US: help@patsnap.com