Charging method used in polyphenylene sulfide production
A feeding method and polyphenylene sulfide technology are applied in the feeding field in the production of polyphenylene sulfide, which can solve the problems of prolonging the reaction time, increasing energy consumption and the like, so as to accelerate the dehydration speed, reduce the loss of raw materials and energy consumption, and reduce the heat. Effect
- Summary
- Abstract
- Description
- Claims
- Application Information
AI Technical Summary
Problems solved by technology
Method used
Examples
Embodiment 1
[0009] Stainless steel 180L reaction kettle, add 40.0kg of solvent NMP and start stirring, add 23.40kg of aqueous sodium sulfide and 3.00kg of catalyst in turn, pass in nitrogen to bring out steam, quickly heat up to remove moisture; after dehydration, stop heating, turn off the protective gas, Quickly add 40.0kg of solvent NMP to the reaction kettle, close the valve of the reaction kettle, and open the feeding valve after the temperature is stable. At this time, the temperature has dropped to 170.2°C, add 22.05kg of p-dichlorobenzene, and finally add 20.0kg of solvent NMP, turn on the heating , into the polymerization reaction stage.
Embodiment 2
[0011] Stainless steel 180L reaction kettle, add 30.0kg of solvent NMP and start stirring, add 23.40kg of aqueous sodium sulfide and 3.00kg of catalyst in turn, pass in nitrogen to bring out steam, quickly heat up to remove moisture; after dehydration, stop heating, turn off the protective gas, Quickly add 50.0kg of solvent NMP to the reaction kettle, close the valve of the reaction kettle, and open the feeding valve after the temperature is stable. At this time, the temperature has dropped to 171.8°C, add 22.05kg of p-dichlorobenzene, and finally add 20.0kg of solvent NMP, turn on the heating , into the polymerization reaction stage.
Embodiment 3
[0013] Stainless steel 180L reaction kettle, add 28.0kg of solvent NMP and start stirring, add 15.60kg of aqueous sodium sulfide and 1.50kg of catalyst in turn, pass in nitrogen to bring out steam, quickly heat up to remove moisture; after dehydration, stop heating, turn off the protective gas, Quickly add 28.0kg of solvent NMP to the reaction kettle, close the valve of the reaction kettle, and open the feeding valve after the temperature is stable. At this time, the temperature has dropped to 167.5°C, add 14.70kg of p-dichlorobenzene, and finally add 14.0kg of solvent NMP, turn on the heating , into the polymerization reaction stage.
[0014] During the implementation of the invention, the dehydration process is rapid and the effect is good. After dehydration, the temperature of the system cools down quickly, avoiding the use of cooling water, reducing energy consumption, and no p-dichlorobenzene escapes during the feeding process, and the subsequent polymerization reaction is...
PUM
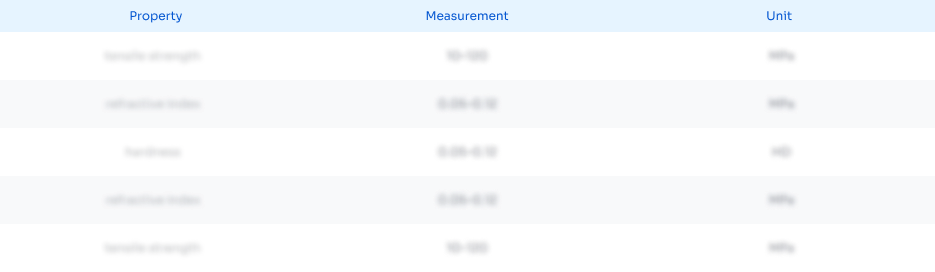
Abstract
Description
Claims
Application Information

- Generate Ideas
- Intellectual Property
- Life Sciences
- Materials
- Tech Scout
- Unparalleled Data Quality
- Higher Quality Content
- 60% Fewer Hallucinations
Browse by: Latest US Patents, China's latest patents, Technical Efficacy Thesaurus, Application Domain, Technology Topic, Popular Technical Reports.
© 2025 PatSnap. All rights reserved.Legal|Privacy policy|Modern Slavery Act Transparency Statement|Sitemap|About US| Contact US: help@patsnap.com