Rim angle excavation method by blasting for natural side hill
A hillside, natural technology, applied in the field of natural hillside corner blasting, can solve the problems of small local space, low efficiency, difficult to deal with, etc., and achieve the effect of increasing economic benefits
- Summary
- Abstract
- Description
- Claims
- Application Information
AI Technical Summary
Problems solved by technology
Method used
Image
Examples
Embodiment 1
[0008] Embodiment 1: the slope of the natural hillside 3 is 30 degrees. At the junction of the natural hillside 3 and the production step 1, a row of vertical holes 2 are drilled with a roller cone drill. The hole distance of the holes is 5 meters, and the hole depth is 16 meters. ; The bottom of the hole is equipped with high-density and high-power explosives, and the millisecond differential blasting is used to break up the natural hillside. After cleaning the rocks, use a down-the-hole drill to drill two rows of horizontal holes from the broken surface 4 after blasting on the remaining irregular triangular natural hillside corners, with a hole spacing of 2 meters and a row spacing of 2 meters; the first row of holes below The height is 0.7 meters from the bottom step, and the hole depth is 8 meters; the depth of the second row of holes is 6 meters, and the rock mass at this part is blasted at one time by using the volley blasting method.
Embodiment 2
[0009] Embodiment 2: the slope of the natural hillside 3 is 45 degrees, and at the junction of the natural hillside 3 and the production step 1, a row of vertical holes 2 are drilled with a roller cone drill. The hole distance of the holes is 5 meters, and the hole depth is 15 meters ; The bottom of the hole is equipped with high-density and high-power explosives, and the millisecond differential blasting is used to break up the natural hillside. Then at the corner part of the natural hillside of the remaining irregular triangle, use the down-the-hole drill to drill two rows of horizontal holes from the broken surface 4 after the explosion, the hole spacing is 2 meters, and the row spacing is 2 meters; the height distance of the first row of holes below The bottom step is 0.5 meters, and the hole depth is 6 meters; the depth of the second row of holes is 4 meters, and the rock mass in this part is blasted at one time by using the volley blasting method.
PUM
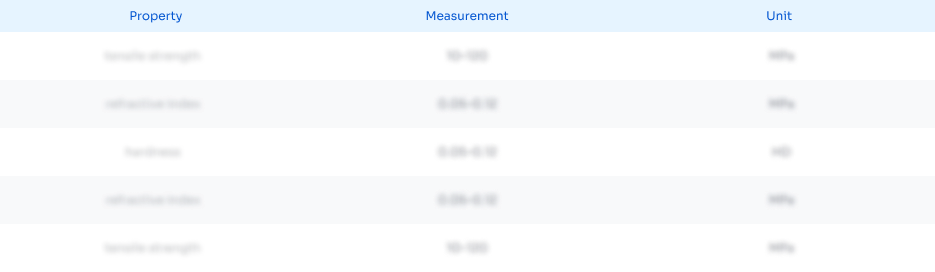
Abstract
Description
Claims
Application Information

- R&D
- Intellectual Property
- Life Sciences
- Materials
- Tech Scout
- Unparalleled Data Quality
- Higher Quality Content
- 60% Fewer Hallucinations
Browse by: Latest US Patents, China's latest patents, Technical Efficacy Thesaurus, Application Domain, Technology Topic, Popular Technical Reports.
© 2025 PatSnap. All rights reserved.Legal|Privacy policy|Modern Slavery Act Transparency Statement|Sitemap|About US| Contact US: help@patsnap.com