Laser welding method, laser welding device, and production method of blower-use impeller
A technology of laser welding and laser irradiation, which is applied in the components, applications, and mechanical equipment of pumping devices for elastic fluids, and can solve problems such as insufficient welding, defective products, and resin burning.
- Summary
- Abstract
- Description
- Claims
- Application Information
AI Technical Summary
Problems solved by technology
Method used
Image
Examples
Embodiment
[0046] Next, an embodiment in which the above-mentioned laser welding method and laser welding apparatus are used in a method of manufacturing an impeller for a blower will be described with reference to the drawings.
[0047] (1) The structure of the impeller for the blower
[0048] Figure 3~ Figure 5 The fan impeller 42 of this embodiment is shown. The blower impeller 42 is an impeller for a turbo fan, and mainly includes: a disc-shaped end plate 43 as a blade supporting rotating body; ) the blade 44 ; and an annular end ring 45 serving as a blade supporting rotating body, which is disposed so as to hold the plurality of blades 44 between the end plate 43 . Here, let O be the center of rotation of the impeller 42 for a blower, and let R be the rotation direction of the impeller 42 for a blower. 3 is an external perspective view of the impeller 42 for a blower. Figure 4 It is the figure which looked at the impeller 42 for blowers from the end ring 45 side. Figure 5 is...
PUM
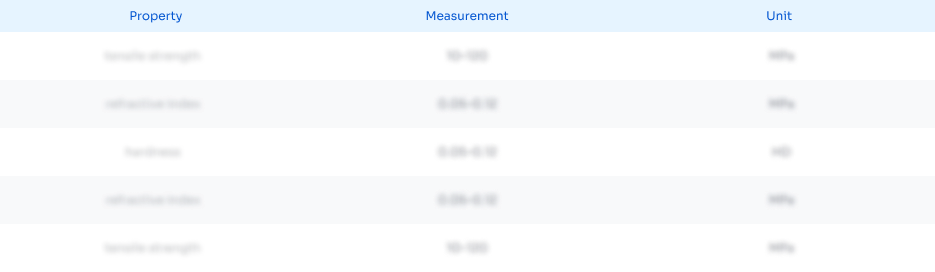
Abstract
Description
Claims
Application Information

- R&D Engineer
- R&D Manager
- IP Professional
- Industry Leading Data Capabilities
- Powerful AI technology
- Patent DNA Extraction
Browse by: Latest US Patents, China's latest patents, Technical Efficacy Thesaurus, Application Domain, Technology Topic, Popular Technical Reports.
© 2024 PatSnap. All rights reserved.Legal|Privacy policy|Modern Slavery Act Transparency Statement|Sitemap|About US| Contact US: help@patsnap.com