Composite spout, and injection molding device for molding the same
A compound nozzle and injection molding technology, which is applied in packaging, transportation and packaging, and other household appliances, and can solve problems such as changes and reduced flavor of the contents
- Summary
- Abstract
- Description
- Claims
- Application Information
AI Technical Summary
Problems solved by technology
Method used
Image
Examples
Embodiment Construction
[0054] Next, the composite nozzle according to the first embodiment of the present invention and the injection molding apparatus for forming the composite nozzle will be described with reference to the drawings.
[0055] In addition, the bushing 10 described in the conventional example is as follows Figure 16 As shown, the multilayer sleeve 10 is composed of five layers including an adhesive layer having the same structure as the sleeve 10 of the present embodiment, and therefore detailed description thereof will be omitted. In addition, the composite nozzle 1 has the side with the discharge opening 6 as the front end side, and the side with the mounting portion 17 as the base end side. The sleeve 10 has the discharge opening 6 side of the composite nozzle 1 as one end portion 10e, and has the attachment portion side of the composite nozzle 1 as the other end portion 10f. In addition, the shape of the sleeve 10 and the orientation of the composite nozzle are the same as in t...
PUM
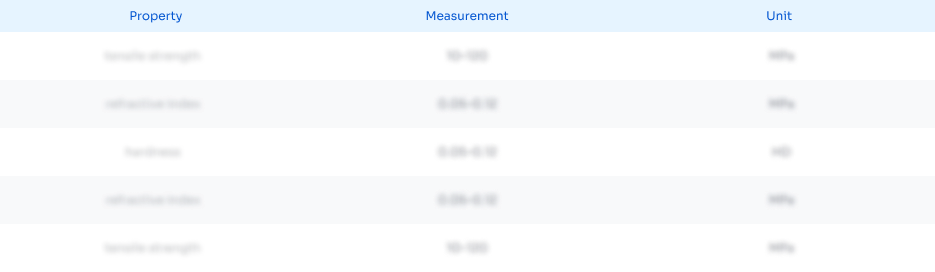
Abstract
Description
Claims
Application Information

- R&D
- Intellectual Property
- Life Sciences
- Materials
- Tech Scout
- Unparalleled Data Quality
- Higher Quality Content
- 60% Fewer Hallucinations
Browse by: Latest US Patents, China's latest patents, Technical Efficacy Thesaurus, Application Domain, Technology Topic, Popular Technical Reports.
© 2025 PatSnap. All rights reserved.Legal|Privacy policy|Modern Slavery Act Transparency Statement|Sitemap|About US| Contact US: help@patsnap.com