Curing formation method for non-flat plate composite product and shaping mould
A composite material and curing molding technology, which is used in the field of curing molding and molding die for non-flat composite material parts, can solve the problems of poor fit between rigid equalizing plates and parts, long working cycle time, etc., and achieves bright arc transition. , Improve work efficiency, smooth folding effect
- Summary
- Abstract
- Description
- Claims
- Application Information
AI Technical Summary
Problems solved by technology
Method used
Image
Examples
Embodiment Construction
[0012] figure 1 An example of a typical cross-sectional composite article made in accordance with the present invention is described.
[0013] exist figure 2 Among them, the flexible soft mold consists of a rigid mold body 1 with the same shape and size as the composite material part 6, and an elastic soft layer 5 placed on the surface of the composite material part 6 blank, and attached to the upper and lower hemming surfaces. , composed of 4 corner pure rubber layers connected by seams. The elastic soft layer 5 is formed by compounding the rubber layer 2 and the fabric layer 3 . The fabric layer 3 can be sandwiched between two rubber layers 2 , and can also be compounded on the inner or outer surface of the rubber layer 2 . The rubber layer material is a rubber whose long-term service temperature is not lower than the curing temperature of the composite material and has excellent heat and oxygen aging resistance. The fabric layer is a fabric whose long-term use temperat...
PUM
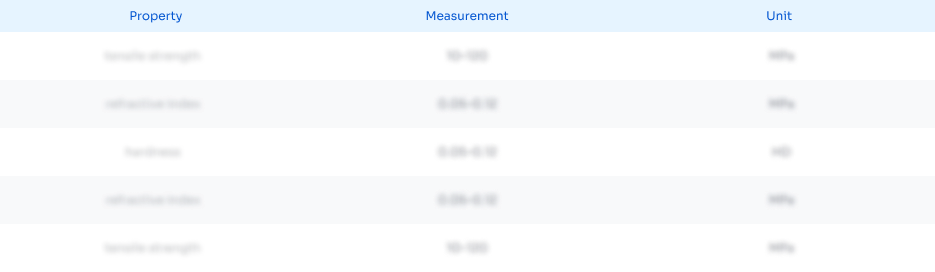
Abstract
Description
Claims
Application Information

- R&D
- Intellectual Property
- Life Sciences
- Materials
- Tech Scout
- Unparalleled Data Quality
- Higher Quality Content
- 60% Fewer Hallucinations
Browse by: Latest US Patents, China's latest patents, Technical Efficacy Thesaurus, Application Domain, Technology Topic, Popular Technical Reports.
© 2025 PatSnap. All rights reserved.Legal|Privacy policy|Modern Slavery Act Transparency Statement|Sitemap|About US| Contact US: help@patsnap.com