Method for preparing high toughness black MC nylon
A high-toughness, black technology, applied in the field of preparation of high-toughness black MC nylon, can solve the problems of high carbon black activity, high brittleness, poor toughness, etc., and achieve the effect of good toughness, good stability and low brittleness of products.
- Summary
- Abstract
- Description
- Claims
- Application Information
AI Technical Summary
Problems solved by technology
Method used
Examples
Embodiment 1
[0023] (1) Preparation of the mold
[0024] a. Clean the mold;
[0025] b. Apply silicone oil release agent on the mold;
[0026] c. Preheat the mold to 155°C;
[0027] (2), configuration of raw materials
[0028] a. Weigh the nylon monomer by weight and place it in the reactor, heat it to 115°C, and vacuum > 99.9kpa until it is completely melted;
[0029] b. Add 2.2 grams of basic catalyst NaOH per kilogram of nylon monomer, heat to 135°C, vacuum > 99.9kpa and boil for 25 minutes;
[0030] c, then add 8 grams of resin ink, add 6 grams of promoter PAPI, 5.4 grams of epoxy resin, mix well;
[0031] (3), pouring and curing
[0032] a. Immediately pour the above-mentioned active raw materials into the mold, heat to 165°C, keep warm for 28 minutes, and then gradually cool down;
[0033] b. Take out the product from the mold and place it in engine oil, keep it warm at 155°C for 2 hours, and cool it together with the engine oil;
[0034] c. Put the product into water and boil...
Embodiment 2
[0036] (1) Preparation of the mold
[0037] a. Clean the mold;
[0038] b. Apply silicone oil release agent on the mold;
[0039] c. Preheat the mold to 165°C;
[0040] (2), configuration of raw materials
[0041] a. Weigh the nylon monomer by weight and place it in the reactor, heat it to 125°C, and vacuum > 99.9kpa until it is completely melted;
[0042] b. Add 2.4 grams of basic catalyst NaOH per kilogram of nylon monomer, heat to 145°C, vacuum > 99.9kpa and boil for 30 minutes;
[0043] c, then add 8 grams of resin ink, add 6 grams of promoter PAPI, 5.4 grams of epoxy resin, mix well;
[0044] (3), pouring and curing
[0045] a. Immediately pour the above-mentioned active raw materials into the mold, heat to 155°C, keep warm for 32 minutes, and then gradually cool;
[0046] b. Take out the product from the mold and place it in engine oil, keep it warm at 150°C for 2 hours, and cool it together with the engine oil;
[0047] c. Put the product into water and boil for ...
Embodiment 3
[0049] (1) Preparation of the mold
[0050] a. Clean the mold;
[0051] b. Apply silicone oil release agent on the mold;
[0052] c. Preheat the mold to 160°C;
[0053] (2), configuration of raw materials
[0054] a. Weigh the nylon monomer by weight and place it in the reactor, heat it to 120°C, and vacuum > 99.9kpa until it is completely melted;
[0055] b. Add 2.3 grams of basic catalyst NaOH per kilogram of nylon monomer, heat to 140°C, vacuum > 99.9kpa and boil for 20 minutes;
[0056] c, then add 8 grams of resin ink, add 6 grams of promoter PAPI, 5.4 grams of epoxy resin, mix well;
[0057] (3), pouring and curing
[0058] a. Immediately pour the above-mentioned active raw materials into the mold, heat to 160°C, keep warm for 0.5 hours, and gradually cool down;
[0059] b. Take out the product from the mold and place it in engine oil, keep it warm at 160°C for 2 hours, and cool it together with the engine oil;
[0060] c. Put the product into water and boil for 2...
PUM
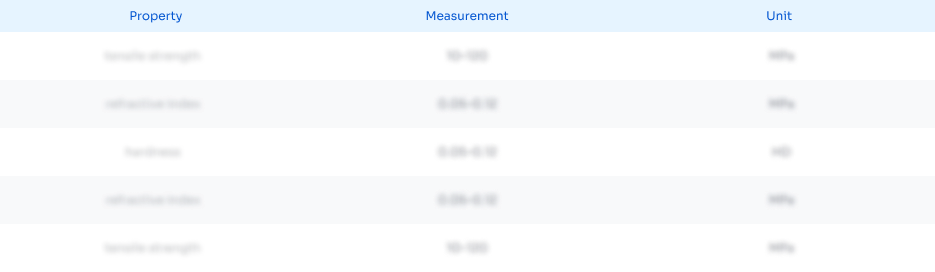
Abstract
Description
Claims
Application Information

- R&D Engineer
- R&D Manager
- IP Professional
- Industry Leading Data Capabilities
- Powerful AI technology
- Patent DNA Extraction
Browse by: Latest US Patents, China's latest patents, Technical Efficacy Thesaurus, Application Domain, Technology Topic, Popular Technical Reports.
© 2024 PatSnap. All rights reserved.Legal|Privacy policy|Modern Slavery Act Transparency Statement|Sitemap|About US| Contact US: help@patsnap.com