Multistage reaction continuous polymerization unit for synthesizing polylactic acid material with lactides monomer
A technology for synthesizing polylactic acid and polymerization equipment, which is applied in the field of multi-stage continuous polymerization technology and equipment, can solve the problems of low conversion rate of lactide, low product molecular weight, difficult operation control, etc., and achieve high molecular weight, excellent physical and mechanical properties, The effect of reducing the load
- Summary
- Abstract
- Description
- Claims
- Application Information
AI Technical Summary
Problems solved by technology
Method used
Image
Examples
Embodiment 1
[0023] Add the refined L-lactide to one of the pre-polymerization tanks. The volume of the pre-polymerization tank is 800L. Remove the original air in the tank and flush it with nitrogen repeatedly. After melting, start the agitator to add catalyst (the amount is 0.1% of the monomer), heat up to 160°C to start polymerization, open the discharge valve when the lactide conversion rate reaches 30%, and prepolymer and remaining lactide are mixed in a certain amount. The speed is put into a twin-screw reaction extruder rotating in the same direction. The diameter of the extruder screw is φ65mm, and the ratio of length to diameter is L / D=45. wait. The lactide conversion rate of the twin-screw reaction extruder reaches about 90%. A melt pump is installed at the outlet of the extruder to control the extrusion rate. About 50-70kg / h of the material passes through the static mixer to make the pre-heated Polymer, lactide, catalyst, etc. are evenly mixed. The static mixer is equipped with...
Embodiment 2
[0025]Add the refined DL-lactide to one of the pre-polymerization tanks. The volume of the pre-polymerization tank is 800L. Remove the original air in the tank and flush it with nitrogen repeatedly. After melting, start the agitator to add the catalyst (the amount is 1% of the monomer), heat up to 180°C to start polymerization, and open the discharge valve when the lactide conversion rate reaches 10%, and the prepolymer and the remaining lactide are mixed in a certain amount. The speed is put into a twin-screw reaction extruder rotating in the same direction. The diameter of the extruder screw is φ65mm, and the ratio of length to diameter is L / D=45. wait. Through the twin-screw reaction extruder until the conversion rate of lactide reaches about 80%, a melt pump is installed at the exit of the extruder to control the extrusion rate, and about 50-70kg / h of the material passes through the static mixer to make it The prepolymer, lactide, catalyst, etc. are evenly mixed. The stat...
Embodiment 3
[0027] Add the mixture of refined DL-lactide and glycolide (the mixing ratio can be determined according to the needs of the product, the ratio in this example is 75:25) into one of the prepolymerization tanks, the volume of the prepolymerization tank is 800L, and the The original air in the kettle was repeatedly flushed with nitrogen, and the temperature was raised to 120-140°C after evacuating and filling several times. After the monomers were completely melted, the agitator was started to add the catalyst (0.01% of the monomer), the molecular weight regulator ethylene glycol (the amount 0.1% of the monomer) to 180 ° C to start polymerization, when the monomer conversion rate reaches 40%, open the discharge valve, put the prepolymer and the remaining monomer into the co-rotating twin-screw reaction extrusion at a certain rate extruder, extruder screw diameter φ65mm, length-to-diameter ratio L / D=45, equipped with forward conveying screw element, kneading block, toothed dispers...
PUM
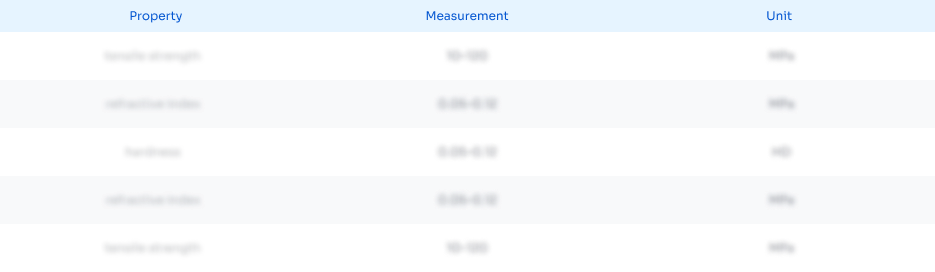
Abstract
Description
Claims
Application Information

- R&D
- Intellectual Property
- Life Sciences
- Materials
- Tech Scout
- Unparalleled Data Quality
- Higher Quality Content
- 60% Fewer Hallucinations
Browse by: Latest US Patents, China's latest patents, Technical Efficacy Thesaurus, Application Domain, Technology Topic, Popular Technical Reports.
© 2025 PatSnap. All rights reserved.Legal|Privacy policy|Modern Slavery Act Transparency Statement|Sitemap|About US| Contact US: help@patsnap.com