Maglev system suspension control method
A levitation control and magnetic levitation technology, which is applied in electric traction, electric vehicles, transportation and packaging, etc., can solve problems such as system instability, system performance deterioration, and difficulty in realizing a magnetic levitation system
- Summary
- Abstract
- Description
- Claims
- Application Information
AI Technical Summary
Problems solved by technology
Method used
Image
Examples
Embodiment Construction
[0018] In order to make the object, technical solution and advantages of the present invention clearer, the present invention will be further described in detail below in conjunction with the accompanying drawings and embodiments. It should be understood that the specific embodiments described here are only used to explain the present invention, not to limit the present invention.
[0019] In order to solve the problem that the PID control method in the prior art can only ensure the optimal suspension control performance under a certain system parameter condition, but the suspension control performance will become worse when the system parameter changes, the present invention proposes a The method of changing the levitation control parameters when the system parameters change can change the levitation control parameters according to the current when the magnetic levitation system is in stable levitation, so that the performance of the levitation system remains unchanged. The i...
PUM
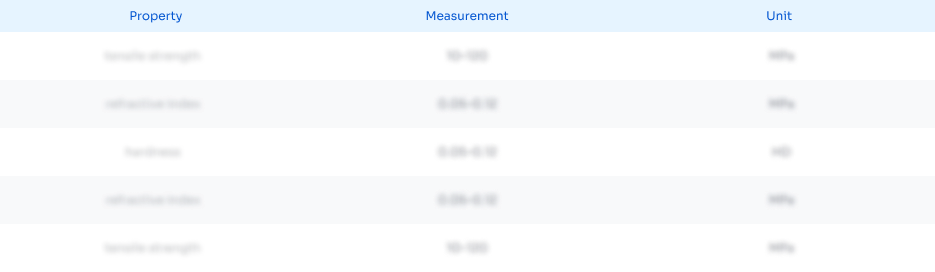
Abstract
Description
Claims
Application Information

- R&D
- Intellectual Property
- Life Sciences
- Materials
- Tech Scout
- Unparalleled Data Quality
- Higher Quality Content
- 60% Fewer Hallucinations
Browse by: Latest US Patents, China's latest patents, Technical Efficacy Thesaurus, Application Domain, Technology Topic, Popular Technical Reports.
© 2025 PatSnap. All rights reserved.Legal|Privacy policy|Modern Slavery Act Transparency Statement|Sitemap|About US| Contact US: help@patsnap.com