Concrete stirring vane die face design system and method based on springback compensation
A mold surface, springback compensation technology, applied in the direction of calculation, special data processing applications, instruments, etc., can solve the problems of difficult mold surface reconstruction, low springback compensation accuracy, and many times of mold repairs, and achieves faster The design process of springback compensation, reducing the number of mold repairs, and improving the effect of springback compensation accuracy
- Summary
- Abstract
- Description
- Claims
- Application Information
AI Technical Summary
Problems solved by technology
Method used
Image
Examples
Embodiment Construction
[0011] Such as figure 1 As shown, the system of the present invention includes three modules: the automatic springback compensation design of the mold surface based on numerical simulation, the CAD reconstruction design of the mold surface, and the mold surface correction based on reverse engineering, and the blade mold surface CAD reconstruction design module 2 is connected to the output of the blade mold surface automatic springback compensation design module 1 based on numerical simulation, and the blade mold surface correction module 3 based on reverse engineering is connected to the output of the blade mold surface CAD reconstruction design module 2 to form a rebound-based Elastic compensation concrete mixing blade mold surface CAD-CAE-CAD integrated system (CAD computer-aided design, CAE computer-aided engineering). Among them, the mold surface automatic springback compensation design module 1 completes the automatic springback compensation design of the blade mold surfa...
PUM
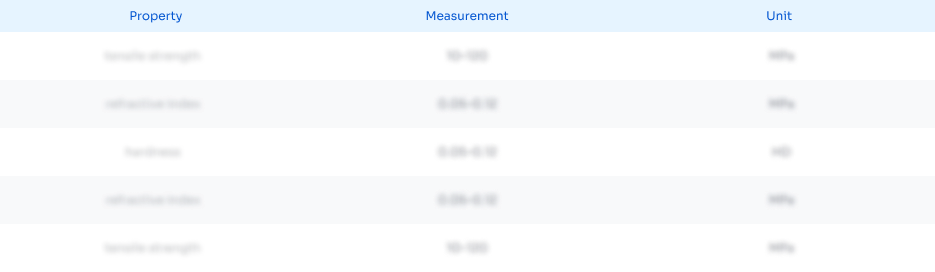
Abstract
Description
Claims
Application Information

- R&D
- Intellectual Property
- Life Sciences
- Materials
- Tech Scout
- Unparalleled Data Quality
- Higher Quality Content
- 60% Fewer Hallucinations
Browse by: Latest US Patents, China's latest patents, Technical Efficacy Thesaurus, Application Domain, Technology Topic, Popular Technical Reports.
© 2025 PatSnap. All rights reserved.Legal|Privacy policy|Modern Slavery Act Transparency Statement|Sitemap|About US| Contact US: help@patsnap.com