Blade wheel of corrosion resistant chemical process pump and its machining process
A processing technology and process pump technology, which is applied in the components, pumps, and applications of pumping devices for elastic fluids, and can solve the problems that cannot completely solve the problem of non-leakage of pump shafts and impellers, shortened service life of equipment, and corrosion of pump internal organs. and other problems, to achieve the effect of beautiful appearance, reducing service life and reducing leakage points of seals
- Summary
- Abstract
- Description
- Claims
- Application Information
AI Technical Summary
Problems solved by technology
Method used
Image
Examples
Embodiment Construction
[0013] from figure 1 It can be seen that a corrosion-resistant chemical process pump impeller is characterized in that: the impeller 1 is made of ultra-high molecular weight polyperfluoroethylene propylene sintered and molded, and the impeller contains a metal bracket 2 inside.
[0014] from figure 2 It can be seen that the processing technology of the impeller is as follows:
[0015] Firstly, the machined metal support 1 and the ultra-high molecular weight polyperfluoroethylene propylene after high-speed centrifugal stirring are injected into the mold to raise the temperature;
[0016] Sintering at a temperature of 370-390°C for 4.5-5.5 hours, then constant temperature at a temperature of 370-380°C for 2.5-3.5 hours and then molding under a pressure of 8-12MPa for 80-120 minutes;
[0017] The molded impeller 2 is demoulded after cooling, put in the natural environment for 110-130 hours, then carries out gold processing, and finally inspects and puts it into storage.
PUM
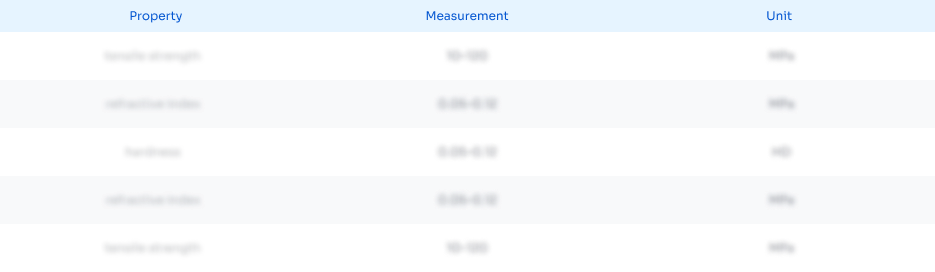
Abstract
Description
Claims
Application Information

- R&D
- Intellectual Property
- Life Sciences
- Materials
- Tech Scout
- Unparalleled Data Quality
- Higher Quality Content
- 60% Fewer Hallucinations
Browse by: Latest US Patents, China's latest patents, Technical Efficacy Thesaurus, Application Domain, Technology Topic, Popular Technical Reports.
© 2025 PatSnap. All rights reserved.Legal|Privacy policy|Modern Slavery Act Transparency Statement|Sitemap|About US| Contact US: help@patsnap.com