Asynchronously and simultaneously implementing rotor variable-frequency control system by semi-bridge inverter driving multiple electric motors
A half-bridge inverter, multi-motor technology, applied in the direction of motor/generator/inverter limiter, motor-generator control, control system, etc., to achieve the effects of cost reduction, energy saving, and volume reduction
- Summary
- Abstract
- Description
- Claims
- Application Information
AI Technical Summary
Problems solved by technology
Method used
Image
Examples
Embodiment Construction
[0058] See Figure 2 and image 3 Shown is a specific embodiment of the present invention.
[0059] Combining Figure 2 and image 3 It can be seen that the present invention consists of a motor group 1, a rectifier group 2, a chopper group 3, an isolator group 4, a current limiting smoother 5, a power capacitor 6, a half-bridge active inverter 7, and a speed feedback device group 8. Current feedback device group 9, excitation transformer 10, excitation contactor 11, control contactor 12, switching contactor 13, driver group 14, microprocessor 15, A / D converter group 16 and signal processor group 17 a whole; of which:
[0060] The motor M in the motor group 1 1 , M 2 , M 3 and M 4 The respective rotors are respectively connected to the Z in the rectifier group 2 in turn 1 ,Z 2 ,Z 3 and Z 4 their corresponding input terminals;
[0061] The output terminal of the half-bridge inverter is connected with the motor M in the motor unit 1 1 , M 2 , M 3 and M 4 The respect...
PUM
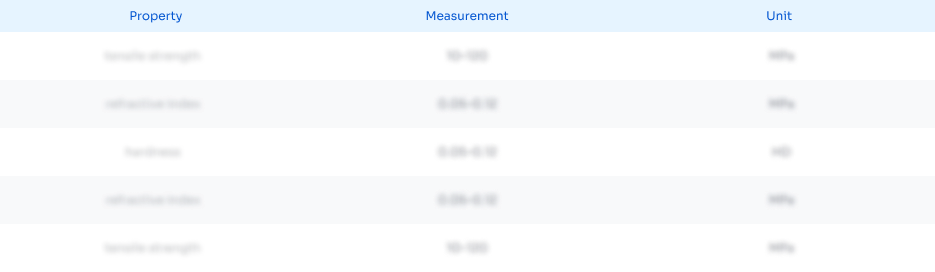
Abstract
Description
Claims
Application Information

- Generate Ideas
- Intellectual Property
- Life Sciences
- Materials
- Tech Scout
- Unparalleled Data Quality
- Higher Quality Content
- 60% Fewer Hallucinations
Browse by: Latest US Patents, China's latest patents, Technical Efficacy Thesaurus, Application Domain, Technology Topic, Popular Technical Reports.
© 2025 PatSnap. All rights reserved.Legal|Privacy policy|Modern Slavery Act Transparency Statement|Sitemap|About US| Contact US: help@patsnap.com