Bidirectional two-speed positioning control method
A positioning control and high-speed technology, applied in the direction of control using feedback, etc., can solve the problems of low positioning control accuracy, lack of elimination of mechanical clearance, and inability to adjust control parameters accordingly
- Summary
- Abstract
- Description
- Claims
- Application Information
AI Technical Summary
Problems solved by technology
Method used
Image
Examples
Embodiment Construction
[0048] image 3 An embodiment of the present invention is given in : the parameter identification process of a side guide plate, wherein the opening and closing of the side guide plate is driven by the rotation of the motor, and the position detection is realized by the encoder. In order to allow the device to move during the parameter identification process, first manually specify any sufficiently large area that the device can move, that is, specify 1 open position OPNpos and 1 closed position CLSpos, and the device is in these 2 positions during the parameter identification process. Moving between locations is accomplished in the following 5 steps:
[0049] Step 1: Move the device from the current position to the open position OPNpos specified during parameter measurement, that is, move the device to the initial position of parameter measurement;
[0050] Step 2: The device starts to close from the current position, and only closes at high speed and moves to the designated...
PUM
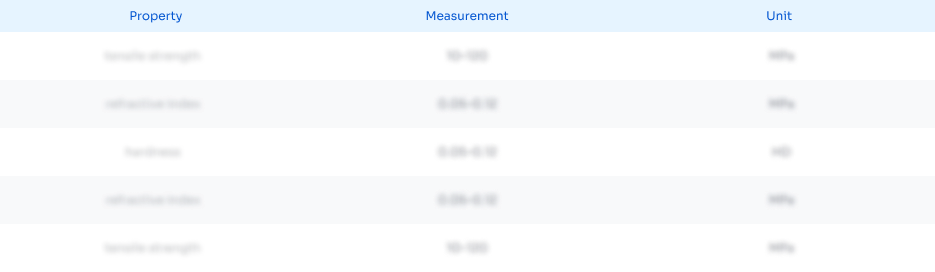
Abstract
Description
Claims
Application Information

- Generate Ideas
- Intellectual Property
- Life Sciences
- Materials
- Tech Scout
- Unparalleled Data Quality
- Higher Quality Content
- 60% Fewer Hallucinations
Browse by: Latest US Patents, China's latest patents, Technical Efficacy Thesaurus, Application Domain, Technology Topic, Popular Technical Reports.
© 2025 PatSnap. All rights reserved.Legal|Privacy policy|Modern Slavery Act Transparency Statement|Sitemap|About US| Contact US: help@patsnap.com