Multi-shaft inertial sensor and method for measuring multi-shaft translation and rotation acceleration
A sensor, axis inertial technology, applied in the sensor field, can solve the problems of high complexity and cost, affecting the development of multi-axis sensor integration, and achieve the effects of large driving dynamic range, easy environmental noise and drift, and low inter-axis crosstalk sensitivity
- Summary
- Abstract
- Description
- Claims
- Application Information
AI Technical Summary
Problems solved by technology
Method used
Image
Examples
Embodiment 1
[0061] A first example consistent with the present invention is shown in figure 1 with figure 2 middle.
[0062] The structure of embodiment one has a square annular outer frame 2, and it will be subjected to figure 2 Driving in the paper direction (ie along the Z axis); four outer elastic beam arms 3 are placed on each outer corner of the frame 2 to play the role of suspending the frame. The four outer elastic beam arms 3 have the same height and extend outward from the bottom surface of the outer frame mass 2 . The inner ring structure of the frame 2 is four mass blocks (4-7), which occupy most of the area of the inner ring of the frame 2. The centers of the four sensing masses occupy four symmetrical positions in frame 2. The four sensing masses in frame 2 have the same level and height. In the exposed structure 1, each sensing mass 4 has four parallel beam arms (41-44) connected to it, and two of the beam arms (41, 44) are connected to the frame and two remote be...
Embodiment 2
[0067] image 3 with Figure 4 A second example consistent with the present invention is given.
[0068] The structure in embodiment two has the outer frame 101 of circular ring, and it will be along the vertical plane on Figure 4 (ie, along the z-axis); four outer elastic beams 102 are used to support the frame 101 . The four outer beams 101 have the same height and extend outward from the bottom surface of the outer beam mass 101 . The four outer beam arms are evenly spaced along the frame. Figure 4 , they are along the X and Y directions. The inner structure of the frame 2 has four sense masses (104-107), which are in the frame 101, have different directions but the same sector shape. The frame 101 and the four inner masses (104-107) have the same height and thickness. The four masses (104-107) form two sensing pairs. The masses 105 and 107 form a pair. The masses 104 and 106 form another pair. In the structure disclosed in this embodiment, the proximal end of a ...
Embodiment 3
[0073] Figure 5 A detailed cross-sectional view of another capacitive motion sensor consistent with this invention is depicted. In this example the structural layer is sandwiched between two base layers forming a differential capacitance.
[0074] with the aforementioned Figure 1-4 Similar to the example in , the structural layer consists of a frame and a mass connected to it by elastic beam arms. In fact, removing the base layer on top, Figure 5 structure in and Figure 1-4 The structure in is very similar. After adding the top base layer and its electrodes, each mass in the structural layer constitutes the central plate in the differential capacitance structure. As the proof mass moves relative to the electrodes in the top and lower layers, one of the differential capacitances increases and the other decreases. The results are Figure 5 The example shown results in higher sensitivity and greater tolerance to temperature variations.
PUM
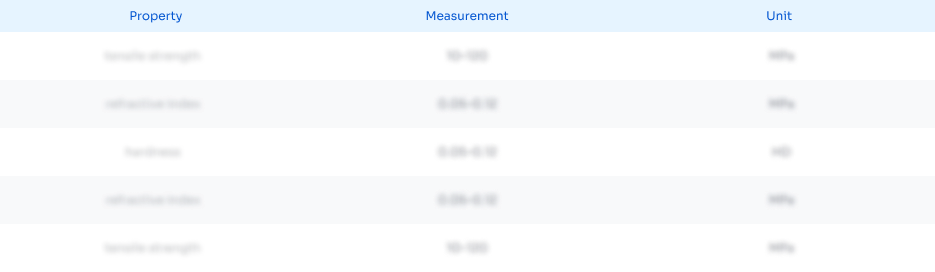
Abstract
Description
Claims
Application Information

- Generate Ideas
- Intellectual Property
- Life Sciences
- Materials
- Tech Scout
- Unparalleled Data Quality
- Higher Quality Content
- 60% Fewer Hallucinations
Browse by: Latest US Patents, China's latest patents, Technical Efficacy Thesaurus, Application Domain, Technology Topic, Popular Technical Reports.
© 2025 PatSnap. All rights reserved.Legal|Privacy policy|Modern Slavery Act Transparency Statement|Sitemap|About US| Contact US: help@patsnap.com