Composite flywheel with plastic blade of engine
A technology combining flywheel and wind impeller, which is applied in the direction of engine cooling, engine components, machine/engine, etc., can solve the problems of scrapped flywheel, high brittleness of cast iron material, broken flywheel blades, etc., to reduce manufacturing cost and simplify casting process , The effect of reducing the scrap rate
- Summary
- Abstract
- Description
- Claims
- Application Information
AI Technical Summary
Problems solved by technology
Method used
Image
Examples
Embodiment Construction
[0011] Below the present invention will be further described in conjunction with the embodiment in the accompanying drawing:
[0012] Such as figure 1 , shown in Fig. 2, mainly comprise flywheel 1, plastic wind impeller 2 (steel bushing 2a), bolt 3 etc.
[0013] In the present invention, the plastic wind impeller 2 is fastened on the screw hole of the flywheel 1 with several bolts 3 . In addition, a steel bushing 2a is cast in the screw hole of the plastic wind impeller 2 to bear the pressing force during locking. In order to prevent the wind impeller 2 from moving radially due to vibration during rotation, the flywheel 1 is processed with a positioning stop circle for the wind impeller. In addition, the two ends of the flywheel 1 and the plastic wind impeller 2 are fitted with inclined planes 4, and the same included angle ensures reliable bonding between the flywheel 1 and the plastic wind impeller 2, effectively preventing the plastic wind impeller 2 from moving radially....
PUM
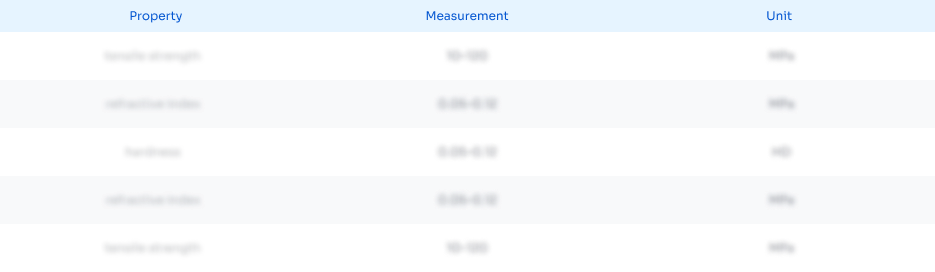
Abstract
Description
Claims
Application Information

- R&D
- Intellectual Property
- Life Sciences
- Materials
- Tech Scout
- Unparalleled Data Quality
- Higher Quality Content
- 60% Fewer Hallucinations
Browse by: Latest US Patents, China's latest patents, Technical Efficacy Thesaurus, Application Domain, Technology Topic, Popular Technical Reports.
© 2025 PatSnap. All rights reserved.Legal|Privacy policy|Modern Slavery Act Transparency Statement|Sitemap|About US| Contact US: help@patsnap.com