Sliding-type constant velocity universal joint
A constant velocity universal joint, sliding technology, applied in the direction of connection, centrifugal force-resistant rotating parts, elastic couplings, etc., can solve the problems of compactness, weight increase and other problems that are light enough
- Summary
- Abstract
- Description
- Claims
- Application Information
AI Technical Summary
Problems solved by technology
Method used
Image
Examples
Embodiment 1
[0032] The DOJ of the present invention does not only have a contact angle of 30° to 35°, but simply forming the contact angle to 30° to 35° will cause an increase in groove surface pressure and a decrease in durability. Therefore, the internal specifications are also changed for other than the contact angle. Table 1 compares the embodiment of the product of the present invention and the conventional product by 5 items. In the present invention, it was confirmed that the DOJ with six balls achieves a size reduction of 3% or more compared to the conventional product.
[0033] 【Table 1】
[0034] project
Product of the present invention
Existing goods
1
(ball diameter) / (outer ring diameter)
0.21~0.25
0.21~0.25
2
(Pitch circle diameter of ball) / (outer ring diameter)
0.64~0.68
0.64~0.68
3
groove contact angle
30~35°
35~40°
4
Groove Contact Ratio
1.02~1.08
1.04~1....
PUM
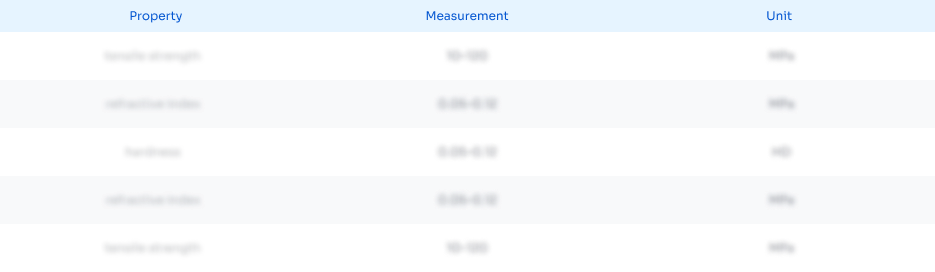
Abstract
Description
Claims
Application Information

- Generate Ideas
- Intellectual Property
- Life Sciences
- Materials
- Tech Scout
- Unparalleled Data Quality
- Higher Quality Content
- 60% Fewer Hallucinations
Browse by: Latest US Patents, China's latest patents, Technical Efficacy Thesaurus, Application Domain, Technology Topic, Popular Technical Reports.
© 2025 PatSnap. All rights reserved.Legal|Privacy policy|Modern Slavery Act Transparency Statement|Sitemap|About US| Contact US: help@patsnap.com