Aluminium alloy manganese additive containing boride
A manganese additive and aluminum alloy technology, which is applied in the field of aluminum alloy manganese additives and additives, can solve the problems of difficulty in controlling the particle size of manganese powder, small and high yield of manganese powder, etc., and achieve less Mn residue and no harmful gas The effect of small amount, good viscosity and surface tension
- Summary
- Abstract
- Description
- Claims
- Application Information
AI Technical Summary
Problems solved by technology
Method used
Examples
Embodiment 1
[0013] Alloy ADC12: Original Mn 0.4wt.%
[0014] Aluminum alloy manganese additive composition (mass percentage): 10% sodium chloride (NaCl), 10% potassium chloride (KCl), 2% sodium fluoroaluminate (NaCl) 3 AlF 6 ), 3% sodium borate (Na 2 B 4 o 7 ), 75% manganese chloride (MnCl 2 ).
[0015] Manganese additive preparation method: Put various raw materials into stainless steel containers respectively, then put the container into an oven, heat up to 200°C with the furnace, keep warm for 2 hours, then take out the materials for use. Each component was accurately weighed according to the formula, ball milled with a ball mill at a speed of 300 rpm for 2 hours, and then dried at 150° C. for 1 hour.
[0016] When in use, when aluminum or aluminum alloy is melted in the smelting furnace and kept warm for a period of time, 0.5% manganese additive is mixed with gas (N 2 or Ar) was sprayed into the melt, and the manganese additive was fully mixed in the entire molten pool. After t...
Embodiment 2
[0018] Alloy ADC12: Original Mn 0.4wt.%
[0019] Aluminum alloy manganese additive composition (mass percentage): 18% sodium chloride (NaCl), 18% potassium chloride (KCl), 8% sodium fluoroaluminate (NaCl) 3 AlF 6 ), 6% sodium borate (Na 2 B 4 o 7 ), 50% manganese chloride (MnCl 2 ).
[0020] Manganese additive preparation method: Put various raw materials into stainless steel containers respectively, then put the container into an oven, heat up to 180°C with the furnace, keep warm for 3 hours, then take out the materials for use. Each component was accurately weighed according to the formula, ball milled for 2 hours with a ball mill at a speed of 300 rpm, and then kept at 200° C. for 2 hours.
[0021] When in use, add 1% manganese additive according to the addition method of Example 1, and keep warm for 10 minutes after adding. The Mn content increased from 0.4% to 0.61%, and the Mn absorption rate was 96%.
Embodiment 3
[0023] Alloy ADC12: Original Mn 0.4wt.%
[0024] Aluminum alloy manganese additive composition (mass percentage): 25% sodium chloride (NaCl), 25% potassium chloride (KCl), 5% sodium fluoroaluminate (NaCl) 3 AlF 6 ), 5% sodium borate (Na 2 B 4 o 7 ), 40% manganese chloride (MnCl 2 ).
[0025] Manganese additive preparation method: Put various raw materials into stainless steel containers respectively, then put the container into an oven, heat up to 150°C with the furnace, keep warm for 3 hours, then take out the materials for use. Each component was accurately weighed according to the formula, ball milled for 1 hour with a ball mill at a speed of 300 rpm, and then kept at 200° C. for 2 hours.
[0026] When in use, add 1.5% manganese additive according to the addition method of Example 1, and keep warm for 5 minutes after adding. The Mn content increased from 0.4% to 0.58%, and the Mn absorption rate was 92%.
PUM
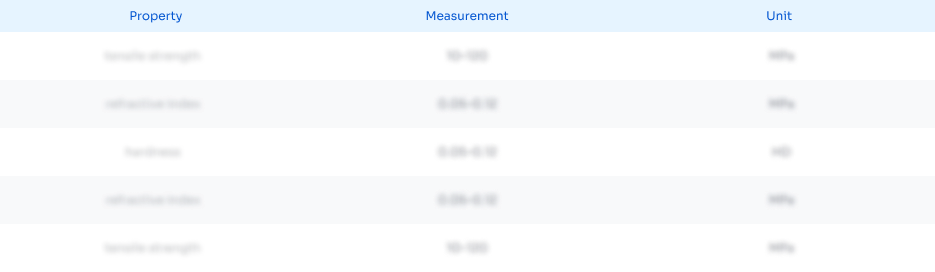
Abstract
Description
Claims
Application Information

- R&D
- Intellectual Property
- Life Sciences
- Materials
- Tech Scout
- Unparalleled Data Quality
- Higher Quality Content
- 60% Fewer Hallucinations
Browse by: Latest US Patents, China's latest patents, Technical Efficacy Thesaurus, Application Domain, Technology Topic, Popular Technical Reports.
© 2025 PatSnap. All rights reserved.Legal|Privacy policy|Modern Slavery Act Transparency Statement|Sitemap|About US| Contact US: help@patsnap.com