Method for forming part with hole
A molding method and part technology, applied in the field of parts molding, can solve problems such as increasing defective rate, affecting part forming quality, tearing, etc., and achieve the effect of reducing defective rate and improving forming quality
- Summary
- Abstract
- Description
- Claims
- Application Information
AI Technical Summary
Problems solved by technology
Method used
Image
Examples
Embodiment Construction
[0014] Next, the method for forming a part with a hole provided by the present invention will be described in detail with reference to the accompanying drawings.
[0015] First, step a): drawing and shaping the sheet. Such as image 3 shown to form figure 1 The part shown is taken as an example. The drawn and shaped part includes a main body 3 and a joint edge 4 connected to the main body 3. The joint edge 4 includes a punching area 5 and a storage material located around the punching area 5. Tendon 6. The punching area 5 is used to form a hole, so the shape and size of the punching area 5 should be consistent with the shape and size of the hole to be formed. The storage ribs 6 are located around the punching area 5, so the location, arrangement and quantity of the storage ribs 6 should be determined according to the punching area 5, that is, the shape of the hole to be formed. For example, due to figure 1 The holes 2 on the part are oblong holes, so the punching area 5 i...
PUM
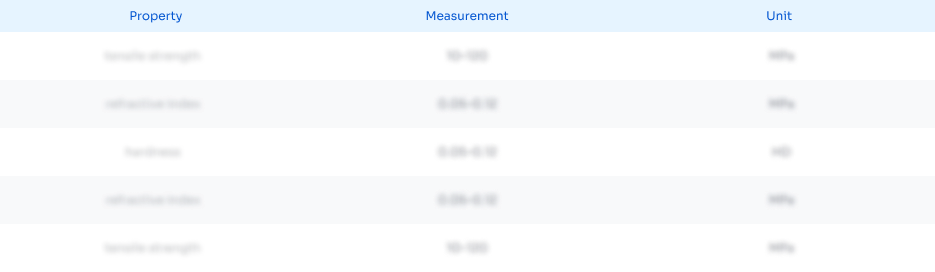
Abstract
Description
Claims
Application Information

- R&D
- Intellectual Property
- Life Sciences
- Materials
- Tech Scout
- Unparalleled Data Quality
- Higher Quality Content
- 60% Fewer Hallucinations
Browse by: Latest US Patents, China's latest patents, Technical Efficacy Thesaurus, Application Domain, Technology Topic, Popular Technical Reports.
© 2025 PatSnap. All rights reserved.Legal|Privacy policy|Modern Slavery Act Transparency Statement|Sitemap|About US| Contact US: help@patsnap.com