Method for reducing vessels stern semi-balance suspension rudder blade surface cavitation
A surface cavitation and semi-balanced technology, which is applied in directions such as rudder steering and steering, can solve the problems of inconvenient draft maintenance, increased propeller load, and drastic changes in wake field, etc., and achieve the effect of reducing cavitation and reducing water flow
- Summary
- Abstract
- Description
- Claims
- Application Information
AI Technical Summary
Problems solved by technology
Method used
Image
Examples
Embodiment Construction
[0026] Next, we take the rudder cavitation model test of a semi-balanced suspended rudder of a 5000TEU class container ship as an example, and describe in detail the method of reducing the cavitation phenomenon on the surface of the rudder blade of the semi-balanced suspended rudder at the stern of the ship. The test was carried out in a cavitation water tank of a ship transportation science research institute.
[0027] See Fig. 2, Fig. 2 is the schematic diagram of the measures taken by the present invention for the cavitation phenomenon at the lower edge of the semi-balanced suspension rudder blade. 1 in the figure is the rudder bearing, and what 2 represents is the rudder blade. The method of the present invention is to change the right angle of the lower edge of the conventional rudder blade into a circular arc, as indicated by the arrow in the figure, the circular arc makes the water flow smoothly transition and reduces the cavitation phenomenon caused by the propeller ti...
PUM
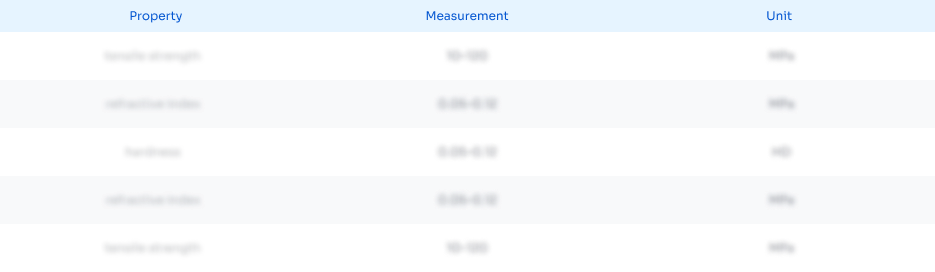
Abstract
Description
Claims
Application Information

- R&D
- Intellectual Property
- Life Sciences
- Materials
- Tech Scout
- Unparalleled Data Quality
- Higher Quality Content
- 60% Fewer Hallucinations
Browse by: Latest US Patents, China's latest patents, Technical Efficacy Thesaurus, Application Domain, Technology Topic, Popular Technical Reports.
© 2025 PatSnap. All rights reserved.Legal|Privacy policy|Modern Slavery Act Transparency Statement|Sitemap|About US| Contact US: help@patsnap.com