Knotting method for integral vacuum circulating degasification furnace vacuum chamber
A technology of vacuum circulation and vacuum chamber, which is applied in the field of the auxiliary working layer of vacuum circulation degassing furnace integral knotting vacuum chamber, can solve the problems that have not been seen, the increase of refining cost, the waste of labor and materials, etc., and achieve the reduction of masonry difficulty and structure Simple, safe to use and reliable results
- Summary
- Abstract
- Description
- Claims
- Application Information
AI Technical Summary
Problems solved by technology
Method used
Image
Examples
Embodiment Construction
[0013] The present invention will be further described below in conjunction with the accompanying drawings.
[0014] As can be seen from the accompanying drawings, the present invention includes a heat insulating layer 4, a heat insulating layer 3, a working layer 1 and a knotting auxiliary working layer 2, and a refractory castable is knotted between the heat insulating layer 2 and the working layer 4 to form an integral vacuum chamber. Knot auxiliary working layer 3. The specific construction process and steps are:
[0015] In the construction of the heat insulation layer 4, in order to ensure the quality of the masonry, the heat insulation board after the masonry is ironed and flattened. According to the size of the vacuum chamber structural part body, the heat insulation board needs to be cut into a suitable size, usually cut into a size It is a square of 200×200mm, and then the cut heat insulation board is pasted on the structural part of the vacuum chamber body with ref...
PUM
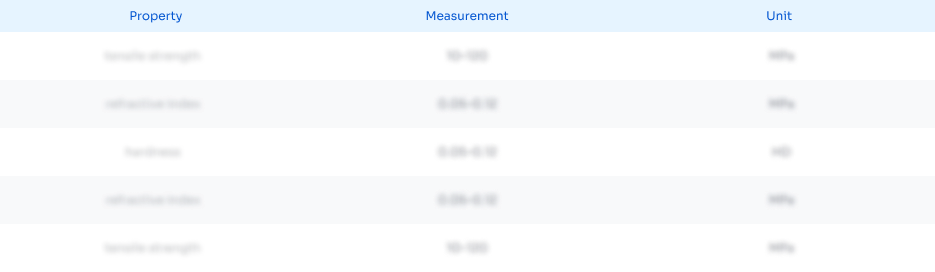
Abstract
Description
Claims
Application Information

- R&D
- Intellectual Property
- Life Sciences
- Materials
- Tech Scout
- Unparalleled Data Quality
- Higher Quality Content
- 60% Fewer Hallucinations
Browse by: Latest US Patents, China's latest patents, Technical Efficacy Thesaurus, Application Domain, Technology Topic, Popular Technical Reports.
© 2025 PatSnap. All rights reserved.Legal|Privacy policy|Modern Slavery Act Transparency Statement|Sitemap|About US| Contact US: help@patsnap.com