Method for preparing nano metallic nickel granular material coating with carbon
A technology of nano-metal and nickel particles, which is applied in the direction of coating, etc., can solve the problems of small controllable range of metal content, small preparation scale, cumbersome operation, etc., and achieve the effect of simple method, single phase and uniform metal particles
- Summary
- Abstract
- Description
- Claims
- Application Information
AI Technical Summary
Problems solved by technology
Method used
Image
Examples
Embodiment 1
[0024] Weigh 7.5g of nickel nitrate hexahydrate, dissolve in about 100ml of ethanol, and stir thoroughly to obtain solution A. Weigh 6.5g of thermosetting epoxy resin, dissolve it in 50ml of ethanol, add 0.7g of polyethylene glycol, mix it with the above-mentioned A solution, stir well, put it in a water bath at 80°C to evaporate the solvent until it is almost dry, and then dry it at 100°C for 4h After pulverization, polymer solids containing metal precursors are obtained. Take 10g of the solid in a porcelain container, place it in the center of the quartz tube in the tube furnace, and 2 Warming up in the air stream, H 2 The flow rate is 40ml / min, the heating rate is 1°C / min, the temperature is raised to 150°C, solidified for 1 hour, and then the temperature is continuously raised to 400°C, and the carbonization is carried out at a constant temperature for 4 hours. After the carbonization is completed, keep the gas flow, cool naturally to room temperature, and obtain a powde...
Embodiment 2
[0026] Weigh 0.62g of nickelocene, dissolve it in 20ml of acetone, stir well, and mix well. Weigh 34.3g of polyethylene resin with a molecular weight of 3000, dissolve it in 150ml of acetone, add 1.75g of methylcellulose, mix with the above solution, stir evenly, evaporate the solvent in a water bath at 80°C until it is nearly dry, dry it at 100°C for about 4 hours, and then pulverize it. Polymer solids containing metal precursors were obtained. Take 10g of the solid in a porcelain container and place it in the center of the quartz tube in the tube furnace. 2 The temperature was raised in the air flow, the flow rate was 40ml / min, the heating rate was 1°C / min, the temperature was raised to 130°C, solidified for 1 hour, and then the temperature was further raised to 600°C, and the carbonization was carried out at a constant temperature for 4 hours. After carbonization, keep the gas flow, cool down to room temperature naturally, and take out the powder sample, which is carbon-...
Embodiment 3
[0028]Weigh 6.4g of nickel acetylacetonate, dissolve it in about 100ml of ethylene glycol, stir well, and mix well. Weigh 31.2g of styrene resin with a molecular weight of 5000, dissolve it in 130ml of ethylene glycol, add 1.87g of methyl cellulose, mix with the above solution, stir evenly, evaporate the solvent in a water bath at 80°C until it is nearly dry, and dry it at 100°C for about 4 hours Pulverize to obtain polymer solids containing metal precursors. Take 10g of the solid in a porcelain container, place it in the center of the quartz tube in a tube furnace, raise the temperature in the He flow, the flow rate is 40ml / min, the heating rate is 1°C / min, the temperature is raised to 140°C, solidified for 1h, and then continue Raise the temperature to 800°C, and carbonize at a constant temperature for 4 hours. After carbonization, keep the gas flow, cool naturally to room temperature, and take out the powder sample, which is the carbon-coated nano-metal nickel particle mat...
PUM
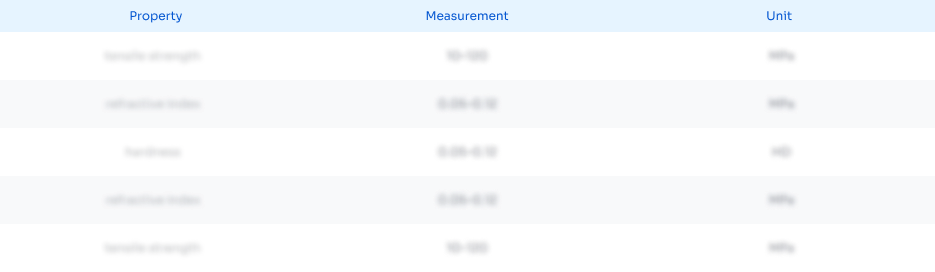
Abstract
Description
Claims
Application Information

- R&D
- Intellectual Property
- Life Sciences
- Materials
- Tech Scout
- Unparalleled Data Quality
- Higher Quality Content
- 60% Fewer Hallucinations
Browse by: Latest US Patents, China's latest patents, Technical Efficacy Thesaurus, Application Domain, Technology Topic, Popular Technical Reports.
© 2025 PatSnap. All rights reserved.Legal|Privacy policy|Modern Slavery Act Transparency Statement|Sitemap|About US| Contact US: help@patsnap.com