Square can and method and device for double-seaming the same
A double hemming and hemming technology, applied in the directions of packaging, transportation and packaging, other household appliances, etc., can solve the problems of unobtainable hemming size and change, and achieve suppression of wrinkles, high sealing performance, and improved storage. The effect of efficiency
- Summary
- Abstract
- Description
- Claims
- Application Information
AI Technical Summary
Problems solved by technology
Method used
Image
Examples
Embodiment 1
[0092] In the device according to the above-mentioned embodiment, the cam groove of the master cam for primary hemming is formed in a shape similar to the outer circumference of the indenter at a predetermined ratio, and the cam groove of the master cam for secondary hemming is formed as follows , that is, the straight line portion is the same as the master cam for the primary curling, but the corner curling portion is as shown in Figure 8, in the cam groove of the primary curling, the centerline of the corner curling portion deviates to the outside by r= The center locus formed by the arc at the position of 0.5mm. In addition, the groove of the secondary hemming roller is set to α=18° and w=3.4 mm in the shape shown in FIG. 7 . In addition, as the indenter, an indenter having a shape as shown in FIG. 4 was used, and the indenter depth was H=2.55 mm.
[0093] According to the above-mentioned device, the can body (material A3003-H14, plate thickness 0.5mm) formed with a radius...
Embodiment 2
[0098] Using the crimping device shown in FIG. 5 and FIG. 9 , primary crimping was performed on a substantially square lid 3 having the following dimensions to obtain a primary crimped square can.
[0099] The shape of the cover before curling: a slightly square shape with one side being 56mm and corner R=8mm
[0100] The shape of the can after one-time crimping: the upper side is 50mm, the corner R is 5mm, and the thickness of the crimping (T(TC) dimension) is 2mm.
[0101] Each dimension of the double seaming device of this embodiment which seamed the square can mentioned above was set as follows.
[0102] Indenter: a slightly square shape with one side 46mm and corner R3mm reduced by the thickness of the crimping of the can.
[0103] The pressing head is arranged at the center of the rotating plate of the curling head.
[0104] Profile cam for primary crimping: a cam with a width of 46mm formed as a roughly square track with a side 120mm drawn from the center of the cam f...
PUM
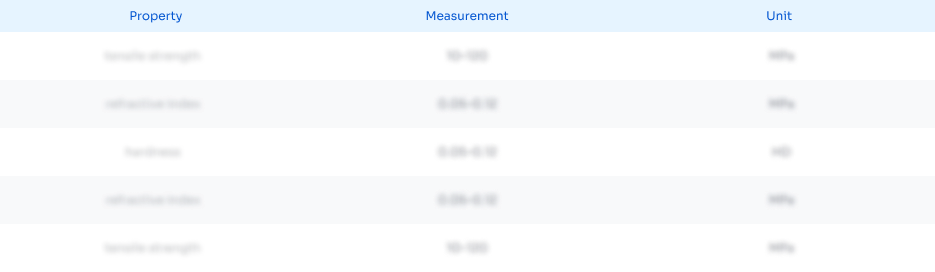
Abstract
Description
Claims
Application Information

- Generate Ideas
- Intellectual Property
- Life Sciences
- Materials
- Tech Scout
- Unparalleled Data Quality
- Higher Quality Content
- 60% Fewer Hallucinations
Browse by: Latest US Patents, China's latest patents, Technical Efficacy Thesaurus, Application Domain, Technology Topic, Popular Technical Reports.
© 2025 PatSnap. All rights reserved.Legal|Privacy policy|Modern Slavery Act Transparency Statement|Sitemap|About US| Contact US: help@patsnap.com