Cylinder-shaped polyphase linear permanent-magnet synchronous generator
A permanent magnet synchronous motor, cylindrical technology, applied in the direction of electrical components, electromechanical devices, electric components, etc., can solve the problem of limited selection, achieve the effect of improving the performance volume ratio, facilitating the processing technology, and increasing the output thrust
- Summary
- Abstract
- Description
- Claims
- Application Information
AI Technical Summary
Problems solved by technology
Method used
Image
Examples
specific Embodiment approach 1
[0009] Specific embodiment one: the cylindrical multi-phase linear permanent magnet synchronous motor of this embodiment includes a primary, a secondary and an air gap, the primary includes an armature core 2 and an armature winding 3, and the armature core 2 is circular, The armature winding 3 is embedded in the slot of the armature core 2, the secondary includes a permanent magnet 4, the permanent magnet 4 is a ring structure, and the tooth pitch τ of the armature core 2 t The pole distance τ from the permanent magnet 4 p Satisfy 0.8τ between t ≤τ p ≤1.2τ t , and τ t ≠τ p this relationship.
[0010] The permanent magnet 4 in the cylindrical multi-phase linear permanent magnet synchronous motor described in this embodiment is a surface permanent magnet structure or an embedded permanent magnet structure.
[0011] The cylindrical multi-phase linear permanent magnet synchronous motor described in this embodiment has a structure in which the primary is sleeved on the outsi...
specific Embodiment approach 2
[0012] Embodiment 2: The difference between this embodiment and the cylindrical multi-phase linear permanent magnet synchronous motor described in Embodiment 1 is that the tooth pitch τ of the armature core 2 t The pole distance τ from the permanent magnet 4 p Satisfy 0.8τ between t ≤τ p t this relationship.
specific Embodiment approach 3
[0013] Embodiment 3: The difference between this embodiment and the cylindrical multi-phase linear permanent magnet synchronous motor described in Embodiment 1 is that the tooth pitch τ of the armature core 2 t The pole distance τ from the permanent magnet 4 p between satisfies τ t p ≤1.2τ t this relationship.
PUM
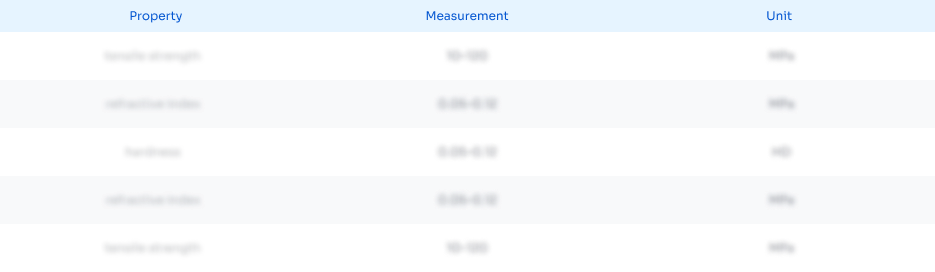
Abstract
Description
Claims
Application Information

- R&D
- Intellectual Property
- Life Sciences
- Materials
- Tech Scout
- Unparalleled Data Quality
- Higher Quality Content
- 60% Fewer Hallucinations
Browse by: Latest US Patents, China's latest patents, Technical Efficacy Thesaurus, Application Domain, Technology Topic, Popular Technical Reports.
© 2025 PatSnap. All rights reserved.Legal|Privacy policy|Modern Slavery Act Transparency Statement|Sitemap|About US| Contact US: help@patsnap.com