Lumber drying kiln
A technology for drying kilns and wood, applied in drying, drying machines, drying solid materials, etc., can solve problems such as affecting market competitiveness, inability to circulate hot air, and low thermal efficiency.
- Summary
- Abstract
- Description
- Claims
- Application Information
AI Technical Summary
Problems solved by technology
Method used
Image
Examples
Embodiment Construction
[0013] As shown in Figure 1 and Figure 2, the wood drying kiln is provided with a partition wall extending from the ground to the kiln wall in the drying kiln. The partition wall divides the space in the kiln into air heating for installing the drying furnace. room 1 and wood drying room 2; the upper part of the partition wall is provided with an upper vent, and the lower part of the partition wall is provided with a lower vent 5, and the upper vent is provided with a The fan 4 for blowing air in the air heating chamber 1; the top kiln wall of the wood drying chamber 2 is provided with an exhaust channel 6 .
[0014] The partition wall includes a vertical wall 3 extending upwards from the ground, a horizontal partition 9 arranged between the top of the vertical wall 3 and the side kiln wall of the air heating chamber 1, and the upper vent 9 is opened on the side kiln wall of the air heating chamber 1. On the horizontal partition 9 described above.
[0015] The partition wall ...
PUM
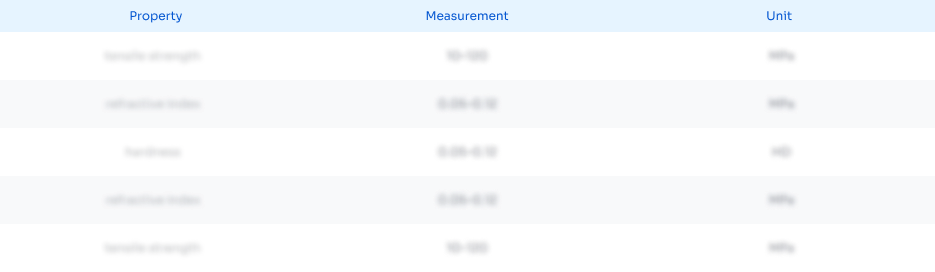
Abstract
Description
Claims
Application Information

- Generate Ideas
- Intellectual Property
- Life Sciences
- Materials
- Tech Scout
- Unparalleled Data Quality
- Higher Quality Content
- 60% Fewer Hallucinations
Browse by: Latest US Patents, China's latest patents, Technical Efficacy Thesaurus, Application Domain, Technology Topic, Popular Technical Reports.
© 2025 PatSnap. All rights reserved.Legal|Privacy policy|Modern Slavery Act Transparency Statement|Sitemap|About US| Contact US: help@patsnap.com