Device used for measuring distance between moving object and its railway
A technology for moving objects and tracks, applied in measuring devices, using electrical devices, and using electromagnetic/magnetic devices to transmit sensing components, etc., can solve the problems of inconvenient maintenance, high cost, inapplicability, etc. low cost effect
- Summary
- Abstract
- Description
- Claims
- Application Information
AI Technical Summary
Problems solved by technology
Method used
Image
Examples
specific Embodiment approach
[0022] Figures 1 to 4 show that a specific embodiment of the present invention is: a device for detecting the distance between a moving object and its orbit, including a signal from a high-frequency signal source entering the sensor, and the signal induced by the sensor by a signal processing circuit to process. The high-frequency signal source S, sensor and signal processing circuit PS are all installed on the moving object, and the sensor is composed of induction winding:
[0023] Each group of induction windings A is composed of four longitudinally arranged induction coils L of the same size wound by a wire, and the winding directions of adjacent induction coils are opposite. The four induction coils are respectively marked as L 1 , L 2 , L 3 , L 4 . The length of the induction winding along the longitudinal direction is equal to twice the longitudinal spacing D of a cycle of the track reluctance or resistance periodic change.
[0024] In this example, the induction wi...
Embodiment 2
[0041] This example is basically the same as the first example, except that the induction winding A is reduced to one group.
Embodiment 3
[0043] This example is basically the same as the first example, except that there are two sets of induction windings A, and one induction coil C for each set. The two sets of windings are staggered along the longitudinal direction of the track, which is half of the period of the track magnetoresistance or resistance length. At any moment during the detection, the magnitude of the change of the high-frequency voltage amplitude generated by the track magnetoresistance or the periodic change of the resistance on the two windings is the same but the direction is opposite.
[0044] The present invention can be used to detect the distance between various objects whose magnetoresistance or resistance changes periodically and the moving objects above them, for example, it can be used to detect the gap between the magnetic levitation vehicle and the magnetic levitation track, so as to ensure the stable suspension and high speed of the magnetic levitation vehicle ,safe operation.
PUM
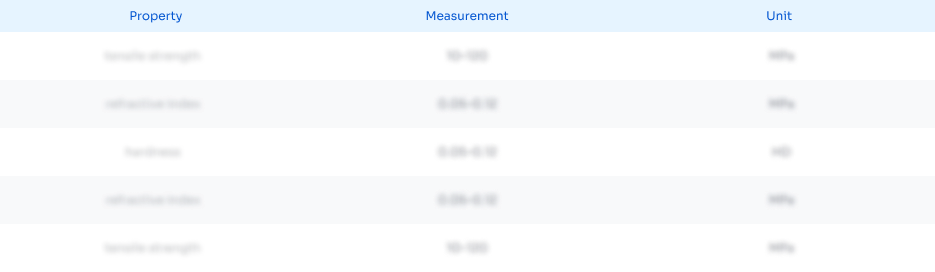
Abstract
Description
Claims
Application Information

- R&D Engineer
- R&D Manager
- IP Professional
- Industry Leading Data Capabilities
- Powerful AI technology
- Patent DNA Extraction
Browse by: Latest US Patents, China's latest patents, Technical Efficacy Thesaurus, Application Domain, Technology Topic, Popular Technical Reports.
© 2024 PatSnap. All rights reserved.Legal|Privacy policy|Modern Slavery Act Transparency Statement|Sitemap|About US| Contact US: help@patsnap.com