Error measuring device of weldless pipe continuous rolling mill roller and detecting method thereof
A technology of deviation detection and seamless pipe connection, which is applied in the direction of measuring device, length measuring device, and fluid device, can solve the problems of many influencing factors, delay in production, and large human factors, so as to ensure rolling quality and measure benchmarks Confirmation, effect of measurement accuracy improvement
- Summary
- Abstract
- Description
- Claims
- Application Information
AI Technical Summary
Problems solved by technology
Method used
Image
Examples
Embodiment Construction
[0019] The present invention will be further described in conjunction with the accompanying drawings.
[0020] The roll deviation detection device of the seamless pipe continuous rolling mill of the present invention mainly detects the deviation of the working surface of the top pocket of the bearing box from the center line of the roll and the deviation of the working surface of the bearing box mounting block from the center of the roll pass. It is composed of two parts: the control conversion system and the detection mechanism. The control conversion system includes a computer, a hydraulic pump station and a displacement sensor installed on the hydraulic cylinder; the detection mechanism is mainly composed of a lifting hydraulic cylinder, a propulsion hydraulic cylinder and a detection frame.
[0021] The computer is equipped with calculation software that converts the data sent by the displacement sensor into a deviation value. The computer is connected with displacement s...
PUM
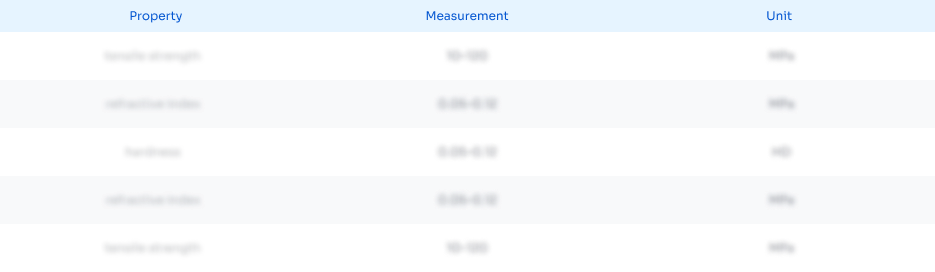
Abstract
Description
Claims
Application Information

- R&D Engineer
- R&D Manager
- IP Professional
- Industry Leading Data Capabilities
- Powerful AI technology
- Patent DNA Extraction
Browse by: Latest US Patents, China's latest patents, Technical Efficacy Thesaurus, Application Domain, Technology Topic, Popular Technical Reports.
© 2024 PatSnap. All rights reserved.Legal|Privacy policy|Modern Slavery Act Transparency Statement|Sitemap|About US| Contact US: help@patsnap.com