Multifunctional barrier-crossing universal magnet wheel robot type working vehicle
A working vehicle and multi-functional technology, applied in the direction of manipulators, manufacturing tools, program control manipulators, etc., can solve the problems of large steering friction, difficulty in maneuvering, reducing magnet adsorption force, etc., to achieve low steering friction and intelligent level High, man-machine communication friendly effect
- Summary
- Abstract
- Description
- Claims
- Application Information
AI Technical Summary
Problems solved by technology
Method used
Image
Examples
Embodiment Construction
[0062] Fix the front-drive horizontal universal multi-group magnet wheels (19) on the front guide car seat plate (16) through the horizontal universal magnet wheel bearing (81) and the horizontal universal magnet wheel lock nut (79), as shown in Figure 17 Show. According to Fig. 6, Fig. 10 scheme, two front auxiliary magnet guide wheels (49), two leading driven rollers (50) and two leading driving magnet rollers (22) are fixed to the end cover (52) through the magnet roller, and fixed On the leading magnet rolling main shaft (53), it is fixed on the magnet rolling fixed mount (23) again, and the magnet rolling fixed mount (23) is fixed to the front guiding main shaft (21) lower end. According to Fig. 2 front guide bearing (24) is put into leading car seat plate (16) front end, and it is fixed on the leading car seat plate (16) with front guide bearing pressure ring (25). After passing the front guide spindle (21) through the front guide bearing (24), tighten the guide bearing...
PUM
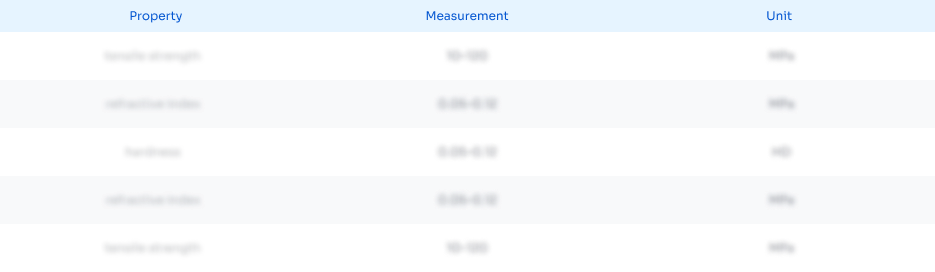
Abstract
Description
Claims
Application Information

- R&D
- Intellectual Property
- Life Sciences
- Materials
- Tech Scout
- Unparalleled Data Quality
- Higher Quality Content
- 60% Fewer Hallucinations
Browse by: Latest US Patents, China's latest patents, Technical Efficacy Thesaurus, Application Domain, Technology Topic, Popular Technical Reports.
© 2025 PatSnap. All rights reserved.Legal|Privacy policy|Modern Slavery Act Transparency Statement|Sitemap|About US| Contact US: help@patsnap.com