Method for solving section temperature difference of broad kiln
A wide-body and cross-section technology is applied in the field of solving the temperature difference of the wide-body kiln cross-section, which can solve the problems of ceramic enterprises such as economic loss, uneven temperature in the firing zone, and large product size difference, so as to shorten the firing cycle and reduce unevenness. The effect of the qualified product rate and the product qualified rate increase
- Summary
- Abstract
- Description
- Claims
- Application Information
AI Technical Summary
Problems solved by technology
Method used
Image
Examples
Embodiment Construction
[0017] Below in conjunction with accompanying drawing and specific embodiment the present invention is described in further detail:
[0018] like figure 1 shown
[0019] figure 1 It is a schematic cross-sectional view of the kiln body firing area in the prior art. exist figure 1 In the process, the product 2 is placed on the porcelain roller 3, and the burner channel 4 of the spray gun passes through the kiln body to the inner wall of the kiln body 1. When the product 2 enters a predetermined position, the flame 5 can only reach the firing zone through the burner channel 4 of the spray gun. At 1 / 4 of the inner diameter of zone 6, this structure requires a large amount of combustion-supporting air, and makes the temperature on both sides of the kiln body 1 relatively high. There is a cross-sectional temperature difference in the kiln body 1, so it takes a long time to increase the temperature of the kiln body 1 firing zone 6. The overall temperature can reach the firing tem...
PUM
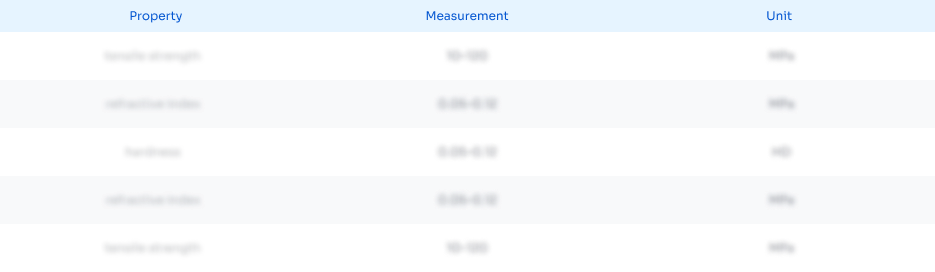
Abstract
Description
Claims
Application Information

- Generate Ideas
- Intellectual Property
- Life Sciences
- Materials
- Tech Scout
- Unparalleled Data Quality
- Higher Quality Content
- 60% Fewer Hallucinations
Browse by: Latest US Patents, China's latest patents, Technical Efficacy Thesaurus, Application Domain, Technology Topic, Popular Technical Reports.
© 2025 PatSnap. All rights reserved.Legal|Privacy policy|Modern Slavery Act Transparency Statement|Sitemap|About US| Contact US: help@patsnap.com