Method of preparing polylactic acid/silicon dioxide nano composite material from acidic silicasol
A technology of nanocomposite material and acidic silica sol is applied in the field of preparing polylactic acid/silica nanocomposite material, which can solve the problems of high cost of silica nanoparticles, high cost of nanoparticles, long route and the like, and achieves low cost, Realize the effect of commercial production and simple process
- Summary
- Abstract
- Description
- Claims
- Application Information
AI Technical Summary
Problems solved by technology
Method used
Image
Examples
Embodiment 1
[0046] Mix 10 grams of acidic silica sol (the amount of silica nanoparticles is 5wt%) and 55.6 grams of 90wt% L-lactic acid aqueous solution under magnetic stirring, and then ultrasonically disperse; , oil bath heating. Dehydrate at 110°C and normal pressure for 2 hours; then gradually reduce the pressure to 0.1atm, raise the temperature to 130°C, dehydrate for 2 hours, and then continue to dehydrate at 150°C and 400Pa for 4 hours to obtain silica containing The lactic acid prepolymer of nanoparticle; 0.23 gram (1mmol) stannous chloride dihydrate and 0.17 gram (1mmol) p-toluenesulfonic acid are joined in this prepolymer, mix well, be warming up to 180 ℃ gradually, gradually Reduce the pressure to 400 Pa, carry out melt polycondensation, and react for 10 hours to obtain a polylactic acid / silicon dioxide nanocomposite material. The yield of polylactic acid is 82.5%, the weight average molecular weight is 70300, and the content of silica nanoparticles is 5.8wt%.
Embodiment 2-7
[0048]0.2 gram, 3 gram, 6 gram, 20 gram, 40 gram, 60 gram of acidic silica sol (silicon dioxide nanoparticle consumption is respectively 0.1wt%, 1.5wt%, 3wt%, 10wt%, 20wt%, 30wt%) Mix with 55.6 grams of 90wt% L-lactic acid aqueous solution under magnetic stirring, and then ultrasonically disperse; then add to a 250mL three-neck round bottom flask, magnetically stir, heat in an oil bath, and dehydrate at 110°C for 2 hours under normal pressure. Then gradually reduce the pressure to 0.1atm, raise the temperature to 130°C, dehydrate for 2 hours, and then continue to dehydrate for 4 hours at 150°C and 400Pa to obtain a lactic acid prepolymer containing silica nanoparticles; (1mmol) tin protochloride dihydrate and 0.17 gram (1mmol) p-toluenesulfonic acid join in the lactic acid prepolymer, mix uniformly, be warming up to 180 ℃ gradually, step down to 400Pa gradually, carry out melting polycondensation, reaction 10 Hours, polylactic acid / silicon dioxide nanocomposites were obtained....
Embodiment 8-10
[0050] 2 grams of silica sol (containing 0.5 grams of silica nanoparticles, and the amount of silica nanoparticles is 1 wt%) was added to 55.6 grams of L-lactic acid aqueous solution, ultrasonically dispersed; transferred to a 250mL three-neck round bottom flask, and magnetically stirred Heated in an oil bath, dehydrated at 110°C and normal pressure for 2 hours, then gradually reduced the pressure to 0.1atm, raised the temperature to 130°C, dehydrated for 2 hours, and then continued to dehydrate at 150°C and 400Pa for 4 hours to obtain Lactic acid prepolymer containing silica nanoparticles. Add 0.23 grams (1 mmol) of stannous chloride dihydrate and 0.17 grams (1 mmol) of p-toluenesulfonic acid into the three-necked flask containing the oligomer, mix well, gradually raise the temperature to 180 ° C, and gradually reduce the pressure to 400Pa, carry out melt polycondensation, and react for 5 hours to obtain a polylactic acid / silicon dioxide nanocomposite material. The yield of ...
PUM
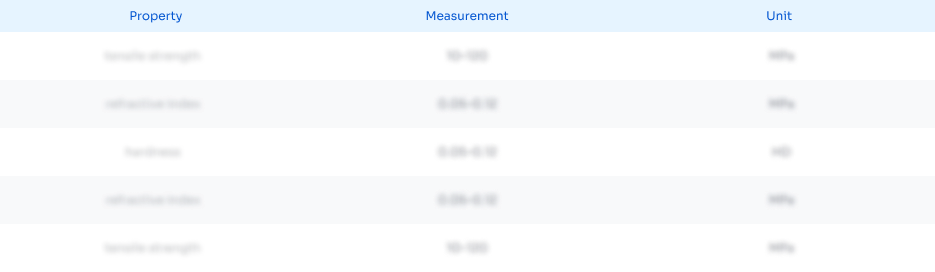
Abstract
Description
Claims
Application Information

- R&D
- Intellectual Property
- Life Sciences
- Materials
- Tech Scout
- Unparalleled Data Quality
- Higher Quality Content
- 60% Fewer Hallucinations
Browse by: Latest US Patents, China's latest patents, Technical Efficacy Thesaurus, Application Domain, Technology Topic, Popular Technical Reports.
© 2025 PatSnap. All rights reserved.Legal|Privacy policy|Modern Slavery Act Transparency Statement|Sitemap|About US| Contact US: help@patsnap.com