Hydrogen production technique
A process, methane technology, applied in the field of new hydrogen production process, to achieve the effect of reducing hydrogen production cost, reducing equipment investment and improving hydrogen production efficiency
- Summary
- Abstract
- Description
- Claims
- Application Information
AI Technical Summary
Problems solved by technology
Method used
Image
Examples
Embodiment 1
[0022] This example is the preparation and pretreatment of the methane carbon dioxide catalytic reforming catalyst A1 in the first step of the hydrogen production process of the present invention.
[0023] Dissolve 29.5g of nickel nitrate, 130g of aluminum nitrate, 0.1g of potassium nitrate, and 290g of magnesium nitrate in 1000ml of deionized water, mix it with ammonia water under stirring, and control the pH to 9±1, filter and wash the resulting precipitate, and put it at 120± Dry at 10°C for 12 hours, and bake at 900±20°C for 10 hours to obtain methane carbon dioxide reforming catalyst A1: NiAl 4.5 K 0.01 Mg 9.2 o 16.96 .
[0024] Take 0.1ml of Catalyst A1 of 40-60 meshes and mix it with 0.3ml of quartz sand evenly, put it into a quartz reactor with a diameter of 5mm and a length of 40mm, purge the reaction system with nitrogen, and then dilute it with nitrogen at a flow rate of 100ml / min. hydrogen, the hydrogen concentration is 10-20% (volume concentration), and the re...
Embodiment 2
[0026] This example is the preparation and pretreatment of the methane carbon dioxide catalytic reforming catalyst A2 in the first step of the hydrogen production process of the present invention. Dissolve 29.5g nickel nitrate, 130g aluminum nitrate, 24.5g cobalt nitrate, 187g zirconium nitrate in 1000ml deionized water, mix with ammonia water under stirring, control pH=9±1, filter and wash the generated precipitate, and put Dry at 10°C for 12 hours, and bake at 900±20°C for 10 hours to obtain methane carbon dioxide reforming catalyst A2: NiAl 4.5 CoZ 5.0 o 13.75 .
[0027] The reduction pretreatment conditions of catalyst A2 were the same as those of catalyst A1 in Example 1.
Embodiment 3
[0029] This example is the preparation and pretreatment of the methane carbon dioxide catalytic reforming catalyst A3 in the first step of the hydrogen production process of the present invention. Dissolve 29.5g nickel nitrate, 130g aluminum nitrate, 0.1g potassium nitrate, 187g zirconium nitrate in 1000m1 deionized water, mix with ammonia water under stirring, control pH=9±1, filter and wash the generated precipitate, and put it at 120± Dry at 10°C for 12 hours, and bake at 900±20°C for 10 hours to obtain methane carbon dioxide reforming catalyst A3: NiAl 4.5 K 0.01 Zr 5.0 o 12.76 .
[0030] The reduction pretreatment conditions of catalyst A3 are the same as the reduction pretreatment conditions of catalyst A1 in Example 1.
PUM
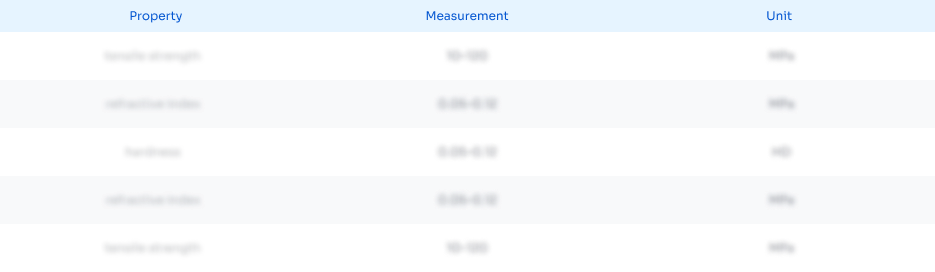
Abstract
Description
Claims
Application Information

- R&D Engineer
- R&D Manager
- IP Professional
- Industry Leading Data Capabilities
- Powerful AI technology
- Patent DNA Extraction
Browse by: Latest US Patents, China's latest patents, Technical Efficacy Thesaurus, Application Domain, Technology Topic.
© 2024 PatSnap. All rights reserved.Legal|Privacy policy|Modern Slavery Act Transparency Statement|Sitemap