Device for clamping components
A component and equipment technology, applied in the field of equipment for welding the components, can solve the problems of high cost, increased heat loss in the seam formation area, and the inability of the planar vacuum clamping table to adapt to different component geometries, etc.
- Summary
- Abstract
- Description
- Claims
- Application Information
AI Technical Summary
Problems solved by technology
Method used
Image
Examples
Embodiment Construction
[0030] figure 1 Shows a perspective view of an exemplary embodiment of the apparatus of the invention for gripping two parts which are to be joined to each other by friction stir welding.
[0031] The device according to the invention comprises, among other elements, a base plate 1 , a base 2 , a solder substrate 3 and holding means 4 , 5 . A plurality of support elements are provided on both sides of the base. The support elements are preferably arranged evenly spaced from each other in a matrix. Such as figure 1 As shown, only half of the support elements 6 to 16 are shown here in order to enhance the graphic representation.
[0032] The first part 17 and the second part 18 are placed on the holding devices 4 , 5 and on the support elements 6 to 16 . The part can be a sheet metal or also a more complex part, such as a part of a fuselage shell or the like.
[0033] The components 17 , 18 are connected in the seam forming region 19 along the component edges 20 , 21 by a w...
PUM
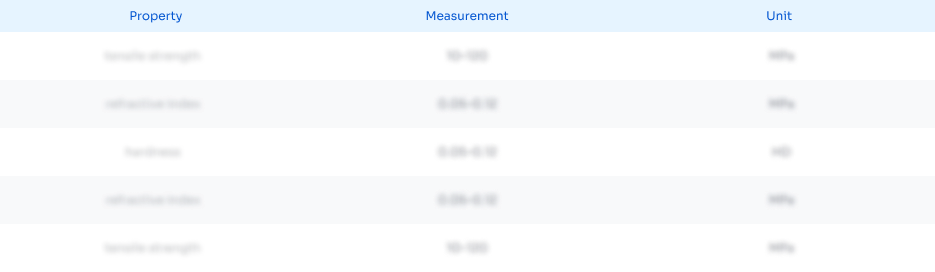
Abstract
Description
Claims
Application Information

- R&D Engineer
- R&D Manager
- IP Professional
- Industry Leading Data Capabilities
- Powerful AI technology
- Patent DNA Extraction
Browse by: Latest US Patents, China's latest patents, Technical Efficacy Thesaurus, Application Domain, Technology Topic, Popular Technical Reports.
© 2024 PatSnap. All rights reserved.Legal|Privacy policy|Modern Slavery Act Transparency Statement|Sitemap|About US| Contact US: help@patsnap.com