Die stamping technique for finished shoes and die stamping equipment
A process and equipment technology, applied in the field of finished shoe molding process and molding equipment, can solve the problems of limiting the development range of molded shoes, easily staining the upper fabric, and affecting the appearance of finished shoes, so as to achieve rich varieties and styles and improve the appearance of finished shoes , The effect of reducing material consumption
- Summary
- Abstract
- Description
- Claims
- Application Information
AI Technical Summary
Problems solved by technology
Method used
Image
Examples
Embodiment Construction
[0016] see figure 1 , the finished shoe molding process of the present invention, the steps are: the shoe last molds 17, 22 for molding are inverted and fixed on the lower workbench 10 of the molding equipment; the bottom mold 16 and the side mold 6 are installed on the upper part of the molding equipment ;Put the spare upper on the shoe last mold; place the filling material, film and accessories according to the shoemaking requirements and paste them on the upper; The side mold and the shoe last mold are pressed together, and the pressure is maintained for molding vulcanization treatment; the pressure is 9-11MPa, and after 8-15 minutes of vulcanization treatment, the side mold is opened, and the bottom mold rises and returns to its original position; finally, the shoe last is taken off , to complete the entire process of molding and pressing shoes.
[0017] In the above process, when entering the molding stage, the initial stage of molding is deflated once or several times a...
PUM
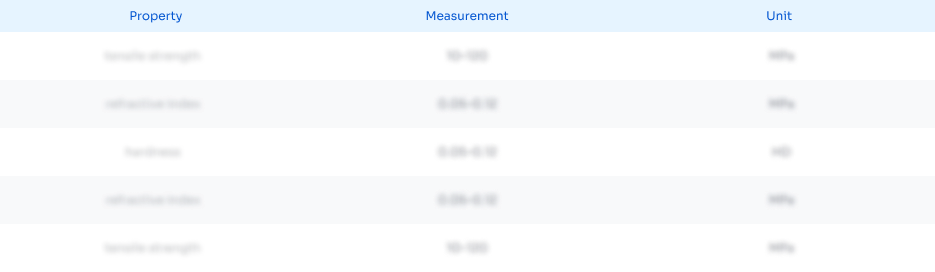
Abstract
Description
Claims
Application Information

- Generate Ideas
- Intellectual Property
- Life Sciences
- Materials
- Tech Scout
- Unparalleled Data Quality
- Higher Quality Content
- 60% Fewer Hallucinations
Browse by: Latest US Patents, China's latest patents, Technical Efficacy Thesaurus, Application Domain, Technology Topic, Popular Technical Reports.
© 2025 PatSnap. All rights reserved.Legal|Privacy policy|Modern Slavery Act Transparency Statement|Sitemap|About US| Contact US: help@patsnap.com