Bionic coupling vibration damper
A shock absorber and steel wire rope technology, which is applied in the field of bionic machinery, can solve the problems of not being able to take into account large shock resistance, vibration and shock resistance, etc., and achieve the effect of small structure, strong versatility, and convenient manufacture
- Summary
- Abstract
- Description
- Claims
- Application Information
AI Technical Summary
Problems solved by technology
Method used
Image
Examples
Embodiment Construction
[0017] Such as figure 1 As shown, in Embodiment 1, a number of steel wire ropes 2 are used to form a cover frame structure, generally 3 to 8 strands are used, and the damping plate 7, the rubber cover 3 and the rubber film 5 form the upper and lower chambers for the oil to flow in series, and the rigidity is extremely small. The rubber membrane 5 and the base 1 form an air squeeze chamber, and the oil 8 can generally adopt silicone oil. In this way, the material and structure are coupled to form a physical structure similar to the characteristics of the head and neck of a woodpecker, so as to achieve bionic anti-vibration by utilizing the superior vibration damping performance of steel wire rope, the superior shock resistance performance of oil damping and the nonlinear adjustment characteristics of air extrusion The goal of the impact protection function.
[0018] Such as figure 2 As shown, embodiment 2 adopts several steel wire ropes to form the crown-shaped cover frame s...
PUM
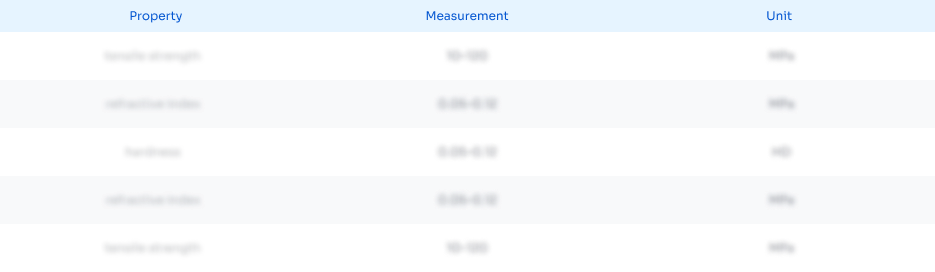
Abstract
Description
Claims
Application Information

- Generate Ideas
- Intellectual Property
- Life Sciences
- Materials
- Tech Scout
- Unparalleled Data Quality
- Higher Quality Content
- 60% Fewer Hallucinations
Browse by: Latest US Patents, China's latest patents, Technical Efficacy Thesaurus, Application Domain, Technology Topic, Popular Technical Reports.
© 2025 PatSnap. All rights reserved.Legal|Privacy policy|Modern Slavery Act Transparency Statement|Sitemap|About US| Contact US: help@patsnap.com