Method of manufacturing outer ring member for constant velocity joint
A technology of constant velocity joints and manufacturing methods, which is applied to engine components, couplings, mechanical equipment, etc., and can solve the problems of increasing the workload of axial end face finishing
- Summary
- Abstract
- Description
- Claims
- Application Information
AI Technical Summary
Problems solved by technology
Method used
Image
Examples
Embodiment Construction
[0031] exist figure 1 The manufacturing process of the outer ring component for the constant velocity joint according to the embodiment of the present invention is shown in . Such as figure 1 As shown in the flow chart of , the workpiece 10 in the form of a carbon steel cylinder is cold-forged five times in total to finally manufacture an outer ring component for a tripod type constant velocity joint.
[0032] exist Figure 2 to Figure 7 The manner in which the shape of the workpiece 10 is changed by the manufacturing process is shown in .
[0033] In a first preparatory step, the workpiece 10 cut into the form of a cylinder having a predetermined length is treated by spheroidizing annealing (see figure 2 ). The workpiece 10 is softened so as to be easy to handle in the first to fifth cold forging steps described below.
[0034] In a second preparatory step, the workpiece 10 is coated with a lubricating chemical film. Specifically, a lubricating chemical film of zinc ph...
PUM
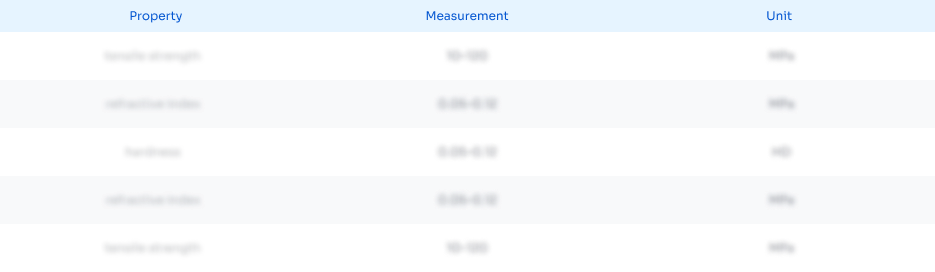
Abstract
Description
Claims
Application Information

- R&D
- Intellectual Property
- Life Sciences
- Materials
- Tech Scout
- Unparalleled Data Quality
- Higher Quality Content
- 60% Fewer Hallucinations
Browse by: Latest US Patents, China's latest patents, Technical Efficacy Thesaurus, Application Domain, Technology Topic, Popular Technical Reports.
© 2025 PatSnap. All rights reserved.Legal|Privacy policy|Modern Slavery Act Transparency Statement|Sitemap|About US| Contact US: help@patsnap.com