Method for producing balling resistant cashmere sweater
A cashmere sweater and anti-pilling technology, applied in textiles and papermaking, fiber treatment, weft knitting, etc., can solve problems such as fluffing and pilling, not effectively restricting fiber movement, and easy fluffing and pilling of finished cashmere sweaters , to achieve the effects of enhanced binding force, improved anti-pilling level, and less prone to pilling
- Summary
- Abstract
- Description
- Claims
- Application Information
AI Technical Summary
Problems solved by technology
Method used
Examples
Embodiment 1
[0040] Example 1, the anti-pilling cashmere cardigan of weft plain stitch is produced with the cashmere yarn whose fineness is 35.7×2tex. Its production process is as follows:
[0041] 1. Selection of cashmere fiber raw materials: select cashmere fiber content of 100%, cashmere fineness of 15μm, length of 33mm;
[0042] 2. Spinning: the fineness of the spun cashmere yarn is: 35.7×2tex, the cashmere single yarn twist: 490 twist / m, twist direction is Z twist; ply twist: 320 twist / m, twist direction is s twist, according to Conventional spinning process for spinning;
[0043] 3. Knitting: On 12-needle horizontal knitting, use 35.7×2tex cashmere yarn to weave the pieces of anti-pilling cashmere cardigan with weft and plain stitches, including: front piece, back piece, sleeve piece, collar piece and placket Wait;
[0044] 4. Garment: According to the style requirements of the cashmere cardigan, the pieces of the cashmere cardigan are sewn into a cashmere cardigan by sewing machi...
Embodiment 2
[0053] Embodiment 2, the anti-pilling cashmere sweater of rib semi-air layer structure is produced with the cashmere yarn that fineness is 38.5 * 2tex. Its production process is as follows:
[0054] 1. Selection of cashmere fiber raw materials: select cashmere fiber content of 100%, cashmere fineness of 15.5μm, length of 31mm;
[0055] 2. Spinning: The fineness of the spun cashmere yarn is: 38.5×2tex, the cashmere single yarn twist: 470 twist / m, twist direction is Z twist; ply twist: 280 twist / m, twist direction is s twist, according to Conventional spinning process for spinning;
[0056] 3. Weaving: On 11-needle horizontal knitting, use 38.5×2tex cashmere yarn to weave the garment parts of anti-pilling cashmere sweater with ribbed semi-air layer structure, including: front piece, back piece, sleeve piece, collar piece, etc.;
[0057] 4. Ready-made garments: According to the style requirements of the cashmere sweater, the pieces of the cashmere sweater are sewn into a cashmere...
Embodiment 3
[0066] Example 3, cashmere vest with anti-pilling weave was produced with cashmere yarn with a fineness of 41.7×2tex. Its production process is as follows:
[0067] 1. Selection of cashmere fiber raw materials: select cashmere fiber content of 100%, cashmere fineness of 16μm, length of 29mm;
[0068] 2. Spinning: The fineness of the spun cashmere yarn is: 41.7×2tex, the cashmere single yarn twist: 460 twist / m, twist direction is Z twist; ply twist: 260 twist / m, twist direction is s twist, according to Conventional spinning process for spinning;
[0069] 3. Weaving: On 10-needle horizontal knitting, use 41.7×2tex cashmere yarn to weave the parts of the anti-pilling cashmere vest with furrow weave, including: front piece, back piece, collar piece and shoulder rib edge, etc.;
[0070] 4. Ready-made garments: according to the style requirements of the cashmere vest, use the sewing machine to sew each piece of the cashmere vest into a cashmere vest;
[0071] 5. Finishing:
[00...
PUM
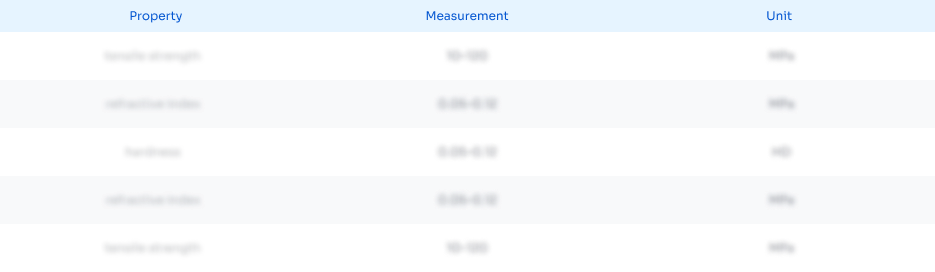
Abstract
Description
Claims
Application Information

- R&D
- Intellectual Property
- Life Sciences
- Materials
- Tech Scout
- Unparalleled Data Quality
- Higher Quality Content
- 60% Fewer Hallucinations
Browse by: Latest US Patents, China's latest patents, Technical Efficacy Thesaurus, Application Domain, Technology Topic, Popular Technical Reports.
© 2025 PatSnap. All rights reserved.Legal|Privacy policy|Modern Slavery Act Transparency Statement|Sitemap|About US| Contact US: help@patsnap.com