Arm mechanism of robot
A technology of robot arm and operating mechanism, which is applied in the direction of manipulators, mechanical equipment, conveyor objects, etc., and can solve problems such as high cost, complicated mechanism, and long connecting rod
- Summary
- Abstract
- Description
- Claims
- Application Information
AI Technical Summary
Problems solved by technology
Method used
Image
Examples
Embodiment Construction
[0035] In the following detailed description, like reference numerals and symbols refer to like components throughout the drawings.
[0036] see figure 1 -4, the figure shows the first embodiment of the robot arm mechanism of the present invention, figure 1 The robot arm mechanism 200 shown in -4 has first and second grippers 214 and 215 respectively supporting and gripping an object.
[0037] The first and second holding members 214 and 215 should be designed, for example, to facilitate holding and releasing wafers or other materials used to manufacture semiconductor parts. First and second clamping members 214 and 215 have first and second end portions respectively, and are made respectively at the first end portion place of second clamping member 214,215 and are designed to be suitable for receiving and releasing described material. The slots 212, 213. The structures of the first and second clamping pieces 214 and 215 depend on the shape and size of the material clamped ...
PUM
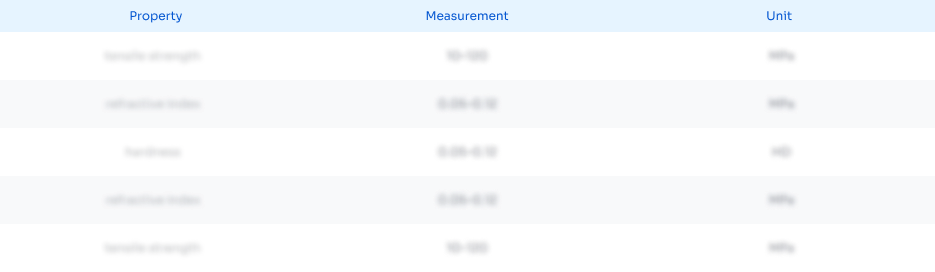
Abstract
Description
Claims
Application Information

- R&D
- Intellectual Property
- Life Sciences
- Materials
- Tech Scout
- Unparalleled Data Quality
- Higher Quality Content
- 60% Fewer Hallucinations
Browse by: Latest US Patents, China's latest patents, Technical Efficacy Thesaurus, Application Domain, Technology Topic, Popular Technical Reports.
© 2025 PatSnap. All rights reserved.Legal|Privacy policy|Modern Slavery Act Transparency Statement|Sitemap|About US| Contact US: help@patsnap.com