Active obstacle travelling robot walking clipping mechanism
A line-following robot and clamping mechanism technology, applied in manipulators, manufacturing tools, etc., can solve the problems of inability to adapt to changes in the angle of overhead ground lines, poor safety protection, and limited obstacle-surmounting ability, and achieve obstacle-surmounting ability and adaptive ability. The effect of strong, light weight and strong obstacle crossing ability
- Summary
- Abstract
- Description
- Claims
- Application Information
AI Technical Summary
Problems solved by technology
Method used
Image
Examples
Embodiment 1
[0030] Such as figure 1 , figure 2 , image 3 , Figure 4 As shown, the present invention is made up of traveling mechanism 1, front clamping mechanism 2, rear clamping mechanism 3, eccentric mechanism 4; Described traveling mechanism 1 is made up of traveling motor 11, traveling wheel 12, left flange 13, traveling wheel support frame 14. Transmission shaft 15, bearing 16, pin 17, and right flange 18 are composed, wherein the travel motor 11 is installed on the left flange 13, and the left flange 13 is connected with the robot operating arm through the sleeve 19 on it, and the left flange 13 is installed on the walking wheel support frame 14, the walking wheel 12 is installed on the transmission shaft 15, the transmission shaft 15 is installed on the support frame 14 through the bearing 16, one end of the transmission shaft 15 is connected with the walking motor shaft through a pin 17, and the right flange 18 is installed on the road wheel support frame 14.
[0031] The f...
PUM
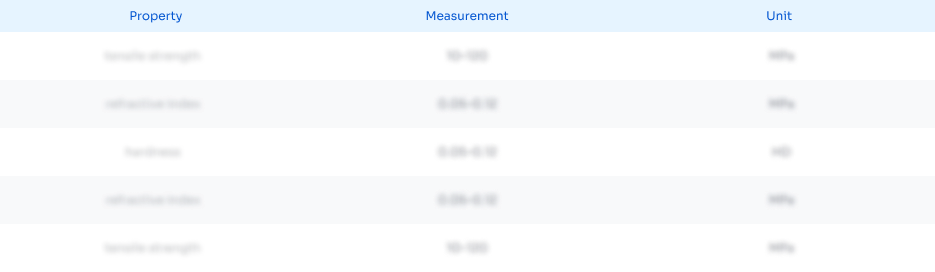
Abstract
Description
Claims
Application Information

- R&D
- Intellectual Property
- Life Sciences
- Materials
- Tech Scout
- Unparalleled Data Quality
- Higher Quality Content
- 60% Fewer Hallucinations
Browse by: Latest US Patents, China's latest patents, Technical Efficacy Thesaurus, Application Domain, Technology Topic, Popular Technical Reports.
© 2025 PatSnap. All rights reserved.Legal|Privacy policy|Modern Slavery Act Transparency Statement|Sitemap|About US| Contact US: help@patsnap.com