Gasifying combined power generating apparatus
A power generation equipment, coal gasification technology, applied in the direction of mechanical equipment, combustion equipment, lighting and heating equipment, etc., can solve the problems of shortening the life of the burner, backflow, gas turbine operation failure, etc.
- Summary
- Abstract
- Description
- Claims
- Application Information
AI Technical Summary
Problems solved by technology
Method used
Image
Examples
no. 1 Embodiment
[0041] The first embodiment (Fig. 1- image 3 )
[0042] FIG. 1 is a system diagram showing the overall structure of a combined coal gasification power generation facility according to an embodiment of the present invention.
[0043] As shown in FIG. 1 , the combined coal gasification power generation equipment of this embodiment generally includes: a gas turbine system 31 ; a fuel supply system 32 ; an air supply system 33 ; an exhaust system 34 and so on.
[0044] The gas turbine system 31 has: a burner 35 capable of selectively combusting coal gasification fuel c and liquid fuel a; a gas turbine 36 driven by combustion gas generated by the burner 35; coaxially arranged with the gas turbine 36 Gas turbine compressor 37 and generator 38.
[0045] The fuel supply system 32 is composed of two systems of a coal gasification fuel supply system 32a and a liquid fuel supply system 32b. The coal gasification fuel supply system 32a has a gasification furnace 39 for gasifying coal ...
no. 2 Embodiment
[0060] The second embodiment ( Figure 4 )
[0061] Figure 4 It is an enlarged cross-sectional view showing the fuel nozzle 65 portion of the burner 35 in the coal gasification fuel combined power generation facility of this embodiment.
[0062] This example Figure 4As shown, on the fuel nozzle 65 that sprays fuel to the burner 35, a liquid fuel flow path 72, an air flow path 73 for atomization, and a coal gasification fuel flow path 74 are arranged in a state of being adjacent to each other. The flow path wall 76 near the outlet of the air flow path 73 for atomization is provided with a spray hole 82 for blowing atomization air into the fuel flow path for coal gasification. The spray holes 82 for the atomization air are formed in a plurality along the circumferential direction of the fuel nozzle 65, and are opened near the discharge ports 80 of the coal gasification fuel flow path 74, for example, continuously spray particles to the inner surface of the swirler 79. Then...
no. 3 Embodiment
[0066] The third embodiment ( Figure 5 )
[0067] Figure 5 It is an enlarged cross-sectional view showing the combustion nozzle 65 of the burner 35 in the combined coal gasification power generation facility of this embodiment.
[0068] This example Figure 5 As shown, at the outlet of the combustion air flow path 63 that blows the combustion air d from the gas turbine compressor 37 (refer to FIG. 1 ) into the combustor sleeve 64, a connection to the coal gasification fuel flow path 74 is provided. The outlet portion is a combustion air ejection portion 83 that ejects combustion air. The combustion air ejection portion 83 includes: for example, a hole 84 pierced on the end wall 64a of the burner sleeve 64 on the combustion nozzle 65 side; The guide member 85 protruding from the inner surface continuously injects the combustion air d to the outside of the swirler 79 of the coal gasification fuel injection port 80 , and an air film can be formed on the coal gasification fu...
PUM
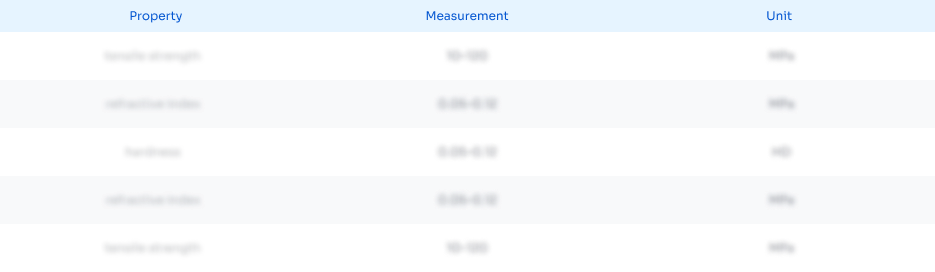
Abstract
Description
Claims
Application Information

- R&D
- Intellectual Property
- Life Sciences
- Materials
- Tech Scout
- Unparalleled Data Quality
- Higher Quality Content
- 60% Fewer Hallucinations
Browse by: Latest US Patents, China's latest patents, Technical Efficacy Thesaurus, Application Domain, Technology Topic, Popular Technical Reports.
© 2025 PatSnap. All rights reserved.Legal|Privacy policy|Modern Slavery Act Transparency Statement|Sitemap|About US| Contact US: help@patsnap.com