One-step reaction method for preparing 4-nitropyridine-nitrogen oxide and halogenated-4-nitropyridine-nitrogen oxide
A technology of halogenated pyridines and nitrogen oxides, which is applied in organic chemistry and other fields, can solve problems such as long reaction time, many steps, and harm to human body, and achieve the effect of shortening reaction time and reducing production cost
- Summary
- Abstract
- Description
- Claims
- Application Information
AI Technical Summary
Problems solved by technology
Method used
Examples
Embodiment 1
[0008] Preparation of 2-chloro-4-nitropyridine-nitrogen oxide:
[0009] (1) Add 2.4 moles of 2-chloropyridine in a 3L three-neck glass flask at room temperature, add about 0.75L of glacial acetic acid while stirring, about 0.9L of 30% hydrogen peroxide or about 0.6L of 50% hydrogen peroxide, and about 0.18L of acetic anhydride, Concentrated sulfuric acid is about 15-20mL, maleic anhydride is about 9g, sodium bisulfate is about 6g, react at 50°C for 0.5 hours, then raise the temperature to 80°C for reaction, the reaction time is 11 hours, and the reaction is complete by thin plate chromatography. Evaporate the solvent under reduced pressure to obtain 2-chloropyridine-nitrogen oxide, which is dark brown solid or viscous; then slowly add about 0.45L of concentrated sulfuric acid and about 12g of sodium nitrate at 15°C, stir to dissolve, and then ℃, add about 0.45L of concentrated sulfuric acid and about 0.75L of fuming nitric acid in batches, and gradually raise the temperature t...
Embodiment 2
[0012] Preparation of 3-chloro-4-nitropyridine-nitrogen oxide:
[0013] (1) Add 2.4 moles of 3-chloropyridine in a 3L three-neck glass flask at room temperature, add about 0.75L of glacial acetic acid, about 0.9L of 30% hydrogen peroxide or about 0.6L of 50% hydrogen peroxide, and about 0.18L of acetic anhydride while stirring, Concentrated sulfuric acid 15-20mL, maleic anhydride 9g, sodium bisulfate 6g, react at 50°C for about 0.5 hours, then raise the temperature to 80°C for reaction, the reaction time is 11 hours, the reaction is complete by thin plate chromatography, and reduce pressure at 65°C Evaporate the solvent to obtain 3-chloropyridine-nitrogen oxide, which is a dark brown solid; then slowly add about 0.45L of concentrated sulfuric acid and about 12g of sodium nitrate at 15°C, stir and dissolve, and then add about 0.45 The mixed acid composed of L concentrated sulfuric acid and about 0.75L fuming nitric acid was gradually heated to about 90°C for reaction, and the r...
Embodiment 3
[0016] Preparation of 2-bromo-4-nitropyridine-nitrogen oxide:
[0017] (1) Add 2.4 moles of 2-bromopyridine in a 3L three-neck glass flask at room temperature, add about 0.75L of glacial acetic acid, about 0.9L of 30% hydrogen peroxide or about 0.6L of 50% hydrogen peroxide, and about 0.18L of acetic anhydride, Concentrated sulfuric acid is about 15-20mL, maleic anhydride 9g, sodium bisulfate 6g, react at 50°C for 0.5 hours, then raise the temperature to 80°C for reaction, the reaction time is 11 hours, thin plate chromatography detects that the reaction is complete, and reduce pressure at 65°C Evaporate the solvent to obtain 2-bromopyridine-nitrogen oxide, which is a dark brown solid; then slowly add about 0.45L of concentrated sulfuric acid and about 12g of sodium nitrate at 15°C, stir and dissolve, and then add about 0.45 The mixed acid composed of L concentrated sulfuric acid and about 0.75L fuming nitric acid was gradually heated to 90°C for reaction, and the reaction tim...
PUM
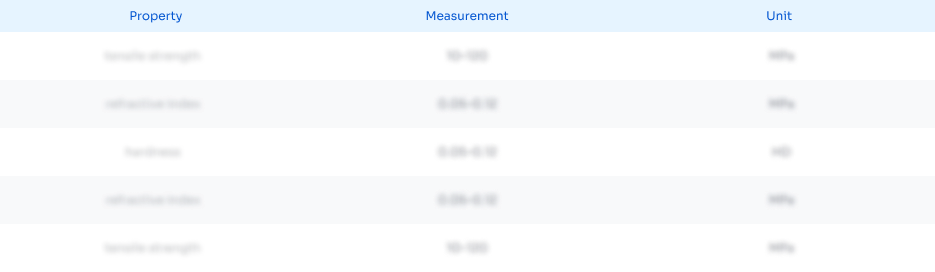
Abstract
Description
Claims
Application Information

- R&D
- Intellectual Property
- Life Sciences
- Materials
- Tech Scout
- Unparalleled Data Quality
- Higher Quality Content
- 60% Fewer Hallucinations
Browse by: Latest US Patents, China's latest patents, Technical Efficacy Thesaurus, Application Domain, Technology Topic, Popular Technical Reports.
© 2025 PatSnap. All rights reserved.Legal|Privacy policy|Modern Slavery Act Transparency Statement|Sitemap|About US| Contact US: help@patsnap.com