Machinery positioning apparatus having independent drive columns
a positioning apparatus and drive column technology, applied in the direction of lifting devices, lifting frames, etc., can solve the problems of wasting a great deal of time, one column to be removed with limited repair skill or specialized mechanical knowledge, etc., to achieve convenient repair and replacement, increase safety and reliability, and improve accuracy and precision. positioning
- Summary
- Abstract
- Description
- Claims
- Application Information
AI Technical Summary
Benefits of technology
Problems solved by technology
Method used
Image
Examples
Embodiment Construction
[0045]FIG. 1 shows a lifting and positioning device 2 having four columns 2000,2100,2200,2300. Each column includes a motor 2020,2120,2220,2320 that rotates a screw (not shown) to move a first support 2010,2110,2210,2310 up and down based on signals received from a controller 4000. The columns are affixed to a base 1000 that may have wheels 1100, 1110 to move the positioning apparatus. It is understood that although the wheels are shown as being adapted to run on rails, wheels that move on other surfaces can be provided. One or both sets of wheels 1100, 1110 can be powered, for example by a motor. In addition, where desirable, one or both sets of the wheels can be adapted to turn to steer the positioning apparatus 2. As shown, wires 2030, 2130,2230, 2330 connect the motors to the controller 4000. It is also understood that the wires may be designed to connect to a power source, and the controller could communicate with the individual motors through a wireless connection. Although sh...
PUM
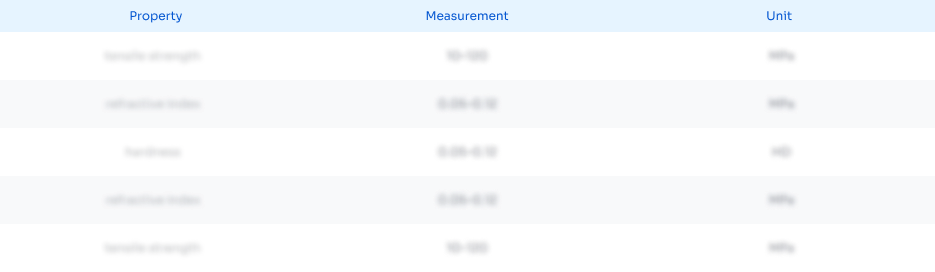
Abstract
Description
Claims
Application Information

- R&D
- Intellectual Property
- Life Sciences
- Materials
- Tech Scout
- Unparalleled Data Quality
- Higher Quality Content
- 60% Fewer Hallucinations
Browse by: Latest US Patents, China's latest patents, Technical Efficacy Thesaurus, Application Domain, Technology Topic, Popular Technical Reports.
© 2025 PatSnap. All rights reserved.Legal|Privacy policy|Modern Slavery Act Transparency Statement|Sitemap|About US| Contact US: help@patsnap.com